Rinsing as it applies to aqueous parts cleaning is a final “cleaning” step which removes residues introduced by or resulting from the primary cleaning process. There are several options to choose from when it comes to rinsing. Making the proper selection is very important to the overall cleaning process as the final rinse inevitably defines overall cleanliness. Despite the importance of good rinsing, “overkill” can be costly and, in some cases, even counter-productive.
The simplest rinse consists of a single tank with a water inlet and a water outlet.
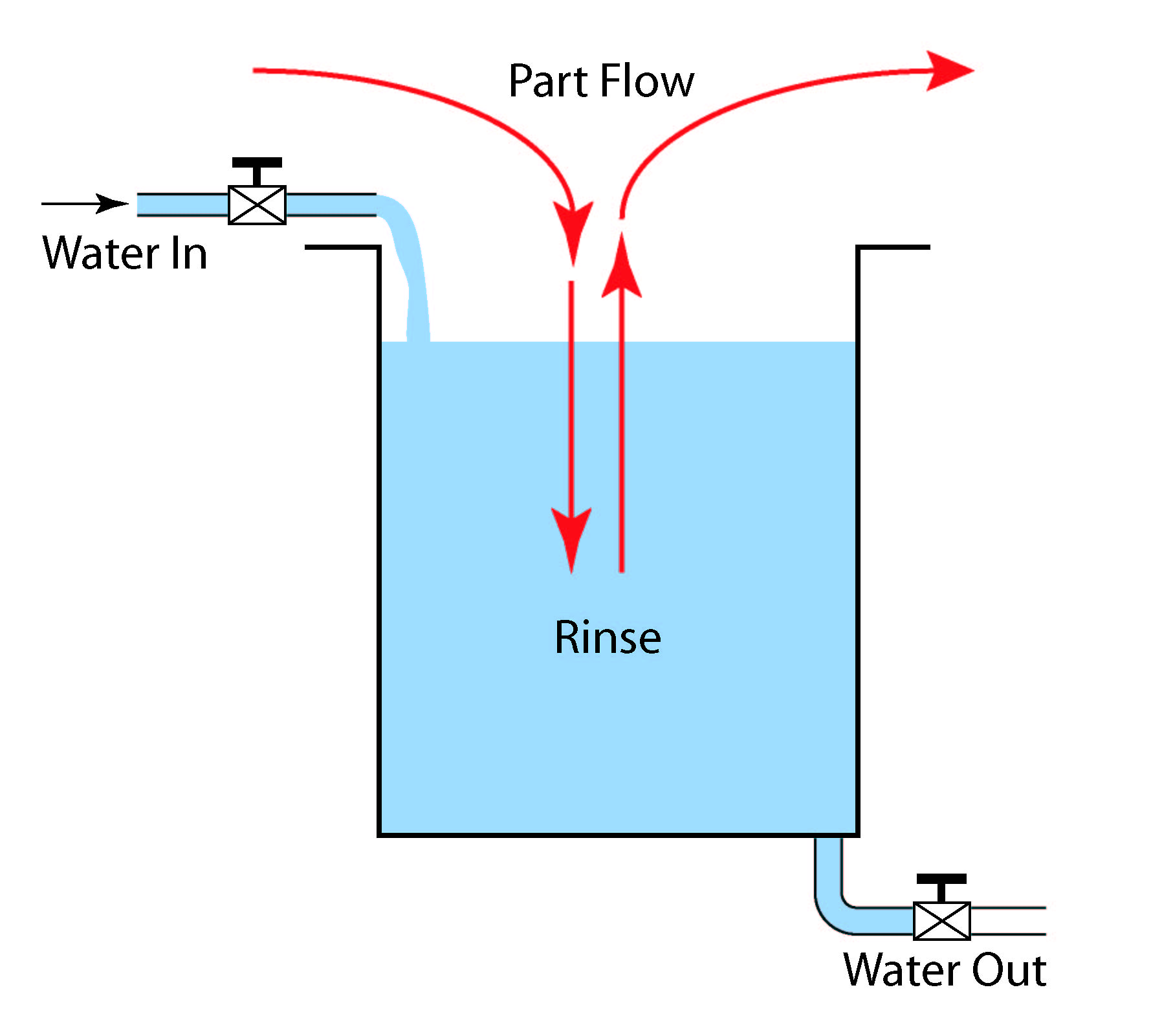
- The rinse is filled, used for a period of time, then drained and re-filled with fresh water. This rinsing scheme, although simple, is wrought with problems and inefficiency. First of all, as soon as parts are introduced into the rinse, contaminates start to build up and the quality of rinsing rapidly degrades. The buildup continues until the rinse is drained and refilled. Although a small amount of contaminant in the rinse may not be harmful (and may even be beneficial as we will see in a later blog), in this case the quality of rinsing varies drastically from the time the rinse is filled until it is drained and refilled. The quality of rinse is totally dependant on the diligence of the operator in replenishing the rinse as needed. Finally, changing the rinse water results in the rinse not being available for a period of time. This is especially true if the rinse water must be heated or if the water source is not able to quickly supply the fresh water (a DI water source, for example) required to re-fill the tank.
- A refinement to the single fill and drain rinse tank is a single tank with a continuous variable water supply and an overflow consisting either of a standpipe or side-mounted overflow fitting.