When a liquid or a gas flows uniformly and without turbulation, the result is called “laminar flow.” The most visual example of laminar flow for most of us are those arching water displays where perfectly shaped slugs of crystal clear water flys gracefully through the air from one point to another.
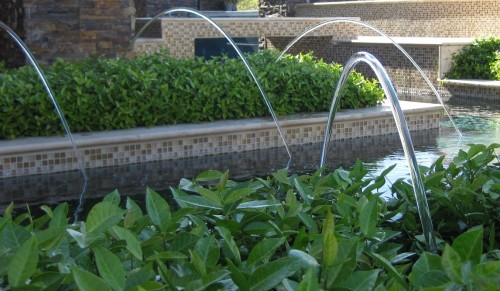
When I first saw this effect at Disney World many years ago, I was confident that they had added something to the water (maybe glycerin?) to make it act that way. I now know that it’s all done by creating a laminar flow. Almost more amazing than the water flying through the air is the fact that there is no splash when the water re-connects with a pool of water at the other end. In cleaning applications, the lack of splash may be the most significant property of laminar flow but it’s not always in a liquid. Let’s dig a little deeper.
By the way, just for fun, try duplicating the above with your garden hose some time – – good luck!
Laminar flow in a tube or pipe means that all of the liquid is moving as a uniform mass at the same speed and in the same direction.
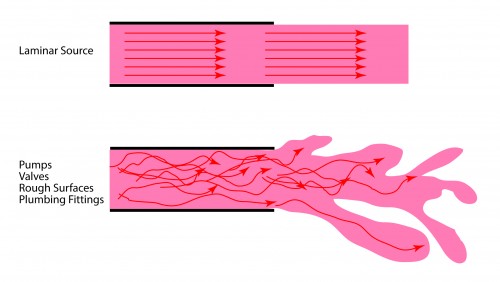
Think flow, not pressure, think low velocity, think smooth, think straight!
Although the above focused on laminar flow in a stream of water, laminar flow is also possible in nearly any confined space as well – tanks, ducts, ovens, etc. Laminar flow is an important design parameter for several applications in industrial cleaning. For example, it is important in rinsing applications where the most efficient exchange of water in a tank is important to minimize water use. In cleaning, laminar flow can help assure that contaminants are removed from the cleaning site so that they can be collected by filtration or disposed of efficiently. In the case of clean rooms, laminar flow of air in laminar flow benches and, in most cases, the entire clean room helps assure that contaminants are not re-distributed into the clean environment. Laminar flow is easier to grasp in concept than it is to produce.Pressure and velocity are enemies to creating laminar flow in both liquids and gasses. Even minor irregularities in the surfaces containing the flow can lead to turbulence fast-moving flows. Smooth walls are therefore important. Ducting or piping should be large with flow rates as low as possible for minimum turbulation and maximum linearity. Nozzles and fans immediately upstream of a space requiring laminar flow are totally contra-indicated. Linearizing flow usually requires a device to straighten the flow. In the case of a gas, laminar flow may be produced by flowing the gas for some distance through a series of parallel small tubes. A pile of drinking straws is often used as an example in laboratory and academic situations. Porous metals, fins/louvers and layers of open cell expanded foam are also practical solutions. Equally important to generating a laminar flow is making sure that it is properly received at the end of its flow. Any obstruction to flow will create turbulation.
In the case of liquids there are a number of schemes to produce laminar flow. In cleaning, laminar flow is usually required in a tank of some description. The use of nozzles (no matter how many) won’t do the job nor will a large number of small holes drilled in a plate with pressurized liquid behind it (which is how a lot of people approach laminar flow). Successful laminar flow can be achieved using porous metal or thicknesses of metal or plastic sponge in line with the flow. In any case, the entire side wall must constitute the source, not just a small window. And again, liquid must be received and removed from the other side of the tank in the same volume as it is introduced and without creating turbulation.
In the design of cleaning machines, laminar flow is something not to be taken lightly or approached without a good understanding of the principles and mechanics involved. It is, as I said above, a little more complex than it sounds and totally counterintuitive but, when used properly, can be a very effective tool.
– FJF –