The last thing you want on a surface that is to be plated, painted or otherwise coated with something that needs to adhere to that surface is a film of residue that prevents that adhesion. The water break test is a simple, quick and usually non-destructive test to test for hydrophobic films. The test is most frequently applied on freshly cleaned metals including steel, aluminum, brass and other metals that, in a totally clean state are hydrophilic.
Although the test is usually applied on large flat surfaces like sheet metal, it can, in somewhat modified form, also be applied to some surfaces with relatively smooth surface geometry. It is not applicable on parts with complex geometry including acute angles and undercuts for example.
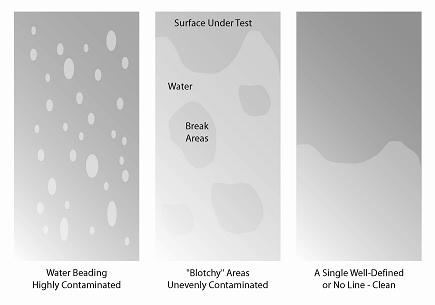
The test is based on the concept that the surface being tested for cleanliness is hydrophilic and the contaminant of concern is hydrophobic in nature. The part being tested is withdrawn relatively rapidly from a bath of clean water – frequently the bath of water is the final rinse of a cleaning process. The film of water on a clean surface will start out as a continuous sheet which will either dry without any discontinuities forming in the film or with a singular defining line which recedes down the surface as the water drains off. Most specifications suggest that the surface being tested by on a 45 degree angle but I have seen the test successfully performed with the surface totally vertical. A surface should not be positioned horizontally for this test.
The water “sheet” on a part that is contaminated with a hydrophobic film will part in the area of the contamination. This break when it occurs is an indication that the surface tension of the water is greater than the force that otherwise would hold it to the hydrophilic surface being tested. There are different ways of interpreting the test. In some cases, any “break” at any time indicates a contaminated surface. In other instances, the time until a “break” in the water sheet is measured in seconds. A “break” within a specified time, often 10 seconds, indicates a contaminated part. On severely contaminated parts, the water will “bead up” in discreet and disconnected beads of various sizes. This test may also be conducted by spraying a part with clean water and, again, watching for a water break in the ways described above.
This test, although quite sensitive when properly performed is also susceptible to some drawbacks. The quality of water used in testing is critical. Small quantities of cleaning chemistry containing soaps or surfactants can prevent a water break from occurring even on a contaminated part. These residues decrease the surface tension of the water thereby allowing the bond to the surface being tested, though it is still contaminated, to be stronger than that of the bond to the water itself. This is one reason why a separate dip tank for the test or a fresh water spray may be preferred to the final rinse in a cleaning system – especially if the quality of the rinse can not be assured. The water break test also may not detect particles that are hydrophilic in nature.
The water break test has served many industries well for many years and is in common use to this day. There are, however, other tests using the same basic idea that we will explore in upcoming blogs.
– FJF –