At the heart of any ultrasonic transducer is a means to convert electrical energy into mechanical energy. The use of piezoelectric materials to do this was discussed in a previous blog. Today’s blog will describe how magnetostrictive materials can also be used to convert electrical energy into mechanical energy.
Ultrasonic transducers using magnetostriction as a source of mechanical or kinetic energy were common in the days between the earliest piezoelectric transducers which, as I explained earlier, were not suitably robust for many applications, and today’s more rugged piezoelectric transducer designs using ceramic rather than crystalline piezoelectric elements. Magnetostrictive ultrasonic transducers still find favor in a few ultrasonic cleaning and other processing applications but have certain limitations which are unlikely to be overcome even with present-day technology which will be discussed in a later blog.
Magnetostrictive materials exhibit a change in volume when subjected to a magnetic field. This is due to the re-arrangement of the magnetic domains within the structure of the material under the influence of a magnetic field. The volume change can be either an increase or a decrease depending on the specific material.
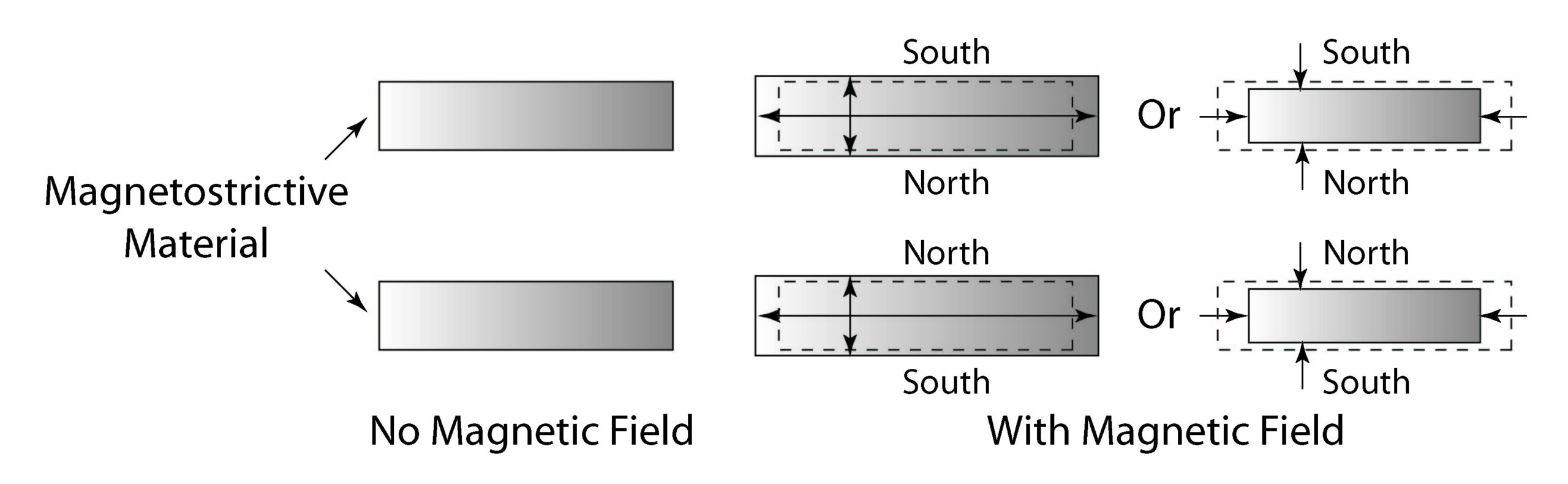
Most materials that can be magnetized exhibit magnetostrictive effects. The magnetostrictive material most commonly used in magnetostrictive ultrasonic transducers is nickel or a nickel alloy. In order to produce the magnetic field required to cause the magnetostrictive material to change volume, a coil of wire is placed near or wrapped around a “stack” of magnetostrive material comprised of many thin laminations similar to those found in electrical transformers. As electricity flows through the coil of wire, a magnetic field is produced which changes polarity each time the flow of current is reversed.
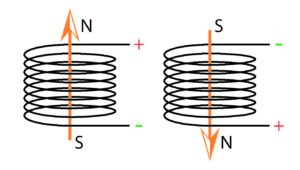
The alternating magnetic field, in turn, causes the magnetostrictive material to expand and contract. Interestingly, the change in volume of the magnetostrictive material is not sensitive to the polarity of the magnetic field. The effect is the same in a North-South oriented field as it is in a South-North oriented field. Because of this, the electrical energy supplied to a magnetostrictive ultrasonic transducer is at 1/2 the desired operating frequency.
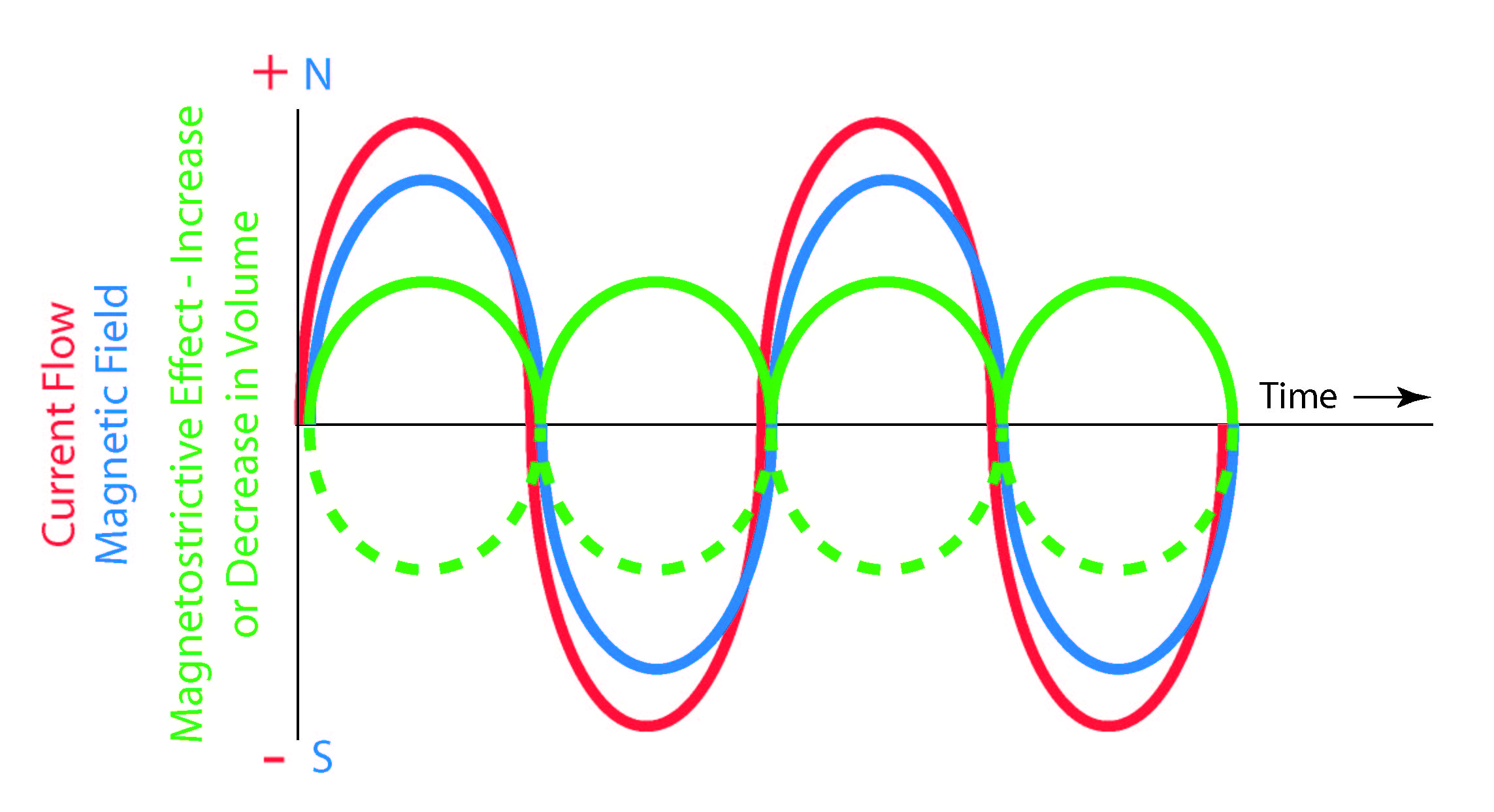
Note – The “hum” we often hear coming from electrical transformers is produced by the magnetosrictive effects on the transformer core laminations as alternating electrical energy flows through the transformer coils. This sound is at a frequency double that of the frequency of the alternating current (for 60 Hz power, the hum is at 120 Hz while for 50 Hz power, the hum is at 100 Hz) since the change in volume of the magnetostrictive material is the same regardless of the polarity of the magnetic field.
Readers may question how a magnetostrictive ultrasonic transducer differs from a common radio speaker. In the radio speaker, a coil of wire produces a magnetic field which acts a stationary magnetic field produced by a permanent magnet. In this arrangement, movement of the coil (which is attached to the speaker cone or radiator) is sensitive to electrical and magnetic polarity and will move one way or the other depending on the polarity of the magnetic field produced by the flow of electrical current in the coil. This arrangement, although it works well for reproducing the sound of music, is not suitable for use in ultrasonic transducers as we will learn in an upcoming blog.
– FJF –