Most cleaning today is based on aqueous (water based) technology. Wash, rinse and dry cleaning has become the norm. But, for those of you who are new to the cleaning industry and don’t know, Chlorinated and Fluorinated solvents were the cleaning “benchmark” for many years. Virtually every manufacturing facility cleaned something using a vapor degreaser with a solvent other than water (water does not work in vapor degreasers). This all changed with the Montreal Protocol which went into effect in 1989. The purpose of the Protocol was to ban or drastically reduce the pollution of the Earth’s atmosphere by the emission of solvents including trichlorotrifluoroethane (Freon TF) and other Fluorinated and Chlorinated Hydrocarbon solvents which had a long residual life once released into the atmosphere. The Protocol and other efforts also sought to reduce the use of solvents which were either proven or suspected to be cancer causing agents and had an adverse environmental effect. In an interesting paradox, it seems the more likely a solvent is to be stable in the atmosphere (thereby creating a problem there), the less likely it is to cause cancer and vice-verse. All of a sudden, nearly all solvents were BAD for one reason or another! But people were in love with solvents and solvent cleaning.
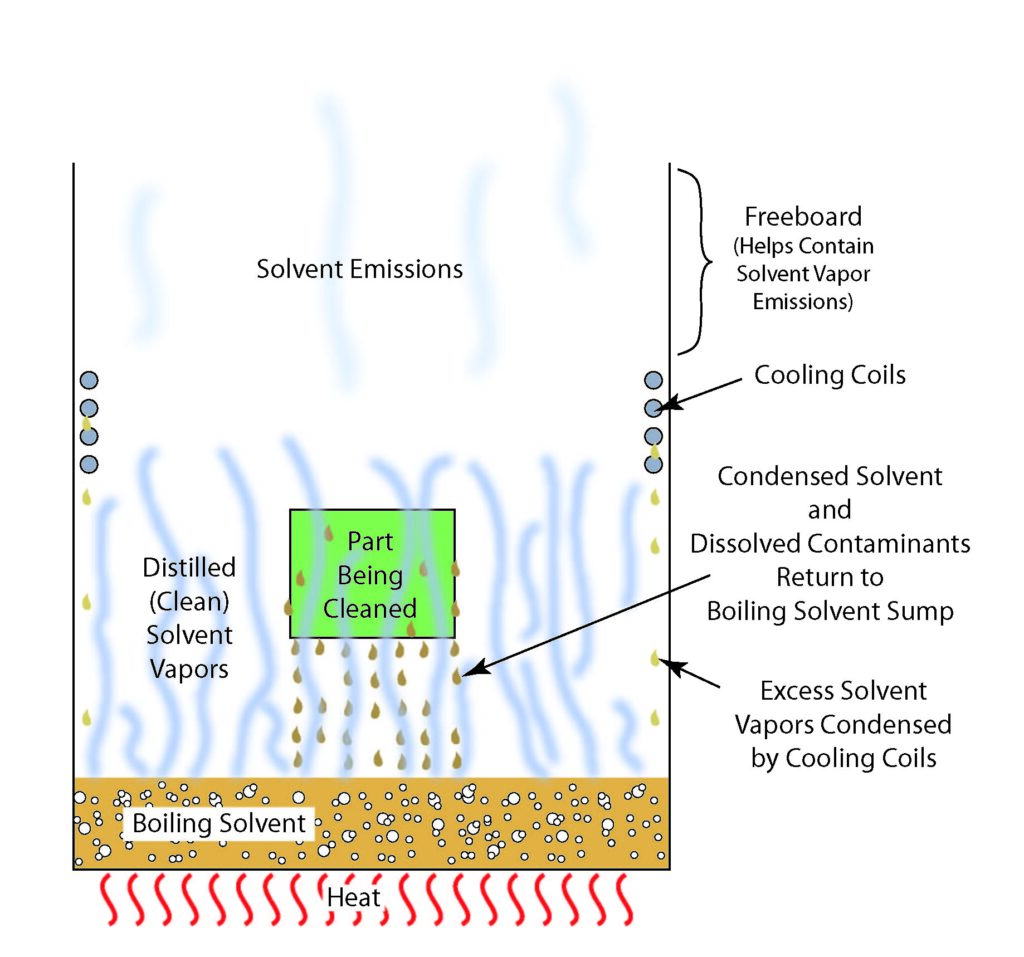
Cleaning using a vapor degreaser was cheap (in part due to the fact that the solvent could be recovered and reused almost indefinitely), fast and easy. The solvent was boiled to produce solvent vapor. Parts were placed in the solvent vapor where the vapor condensed on the surface of the parts (which were cooler than the vapor). The hot, condensed solvent dissolved and took with it grease, oil and other contaminants in a single step process and returned it along with the contaminants back to the bottom of the vessel where it collected. Cleaning was complete when the part reached the boiling temperature of the solvent and solvent no longer condensed on its surface. The clean, hot part was removed slowly from the solvent vapors allowing any condensed solvent remaining on its surface to vaporize and, hopefully, be condensed by cooling coils and returned to the boiling tank. At the bottom of the degreaser, the solvent, having a lower boiling temperature than the contaminants, was then boiled off (distillation) to form new, contaminant-free vapor. Vapor degreasing using solvents had the benefit that the solvent could be distilled and re-used almost endlessly. The problem was that vapor of the solvents that inevitably escaped into the atmosphere were found to remain there for decades and decades with serious effects including their contribution to the formation of the now famous “Hole in the Ozone Layer.”
The strict regulation and banning of solvents caused a major uproar in the cleaning industry. All of a sudden, hundreds of thousands of vapor degreaser users had to find an alternative means of cleaning using less (or no) solvent. The motivation was not only the Protocol, but the sky-rocketing price of solvent caused by its provisions. The first response of users was to implement know means of preventing vapor loss including automated covers, increased freeboard height, better cooling (to prevent the emission of excess solvent vapors into the atmosphere), automation to control the speed of movement of parts into and out of the solvent vapor, and improved controls to detect and prevent solvent loss. In many cases, these measures, although they were known to reduce solvent emissions, were not previously implemented because of cost or ignorance. In the end, however, solvents either needed to be eliminated or contained. The problem was not that the solvents existed but that they weren’t being adequately contained and controlled. Solvent vapors, after all, can not be seen and many have little or no odor in the concentrations that constitute significant emissions.
Interestingly, although the Montreal Protocol had a major impact on the cleaning industry, the emission of solvents in cleaning applications accounted for only a very small percentage of overall solvent emissions. These solvents were also used as propellants (the pressure in spray paint cans) and “blowing agents” (things that make Styrofoam “foam”) for example. The cleaning industry alone was not responsible for the problem of solvents in the atmosphere but, in many ways, took the greatest hit when they were banned as the industry changed completely in the “blink of an eye.”
Upcoming blogs will discuss how people used water to achieve cleaning proven better than that previously achieved using solvents and how solvents may be staging a come-back in the cleaning industry today.
– FJF –