Today’s ultrasonic transducers utilize either the piezoelectric or magnetostrictive effect of materials to produce ultrasonic waves in liquids. This blog will concentrate on the magnetostrictive ultrasonic transducer.
Magnetostrictive Transducers –
Magnetostrictive ultrasonic transducers utilize the principle of magnetostriction exhibited by “ferromagnetic” materials which include iron, nickel and cobalt as well as many alloys of these three elements to create ultrasonic waves in a liquid. The magnetostrictive principle was described in some detail in a previous blog. Additional information on magnetostriction and ferromagnetism can be found in a “reader friendly” paper entitled Magnetostrictive Materials Background written by Geoffrey P. McKnight of the UCLA Active Materials Lab. Devices to create motion using the principle of magnetostriction were first developed in the 1930’s and perhaps earlier although earlier work was not exploited. In the 1940’s and 1950’s, the technology expanded into the ultrasonic frequency range in response to a need for ultrasonic devices that were more robust than those using the (then) fragile crystal compositions that were used in piezoelectric ultrasonic transducers of the day. Some of the developmental work on magnetostrictive transducers in the 1950’s was done by Alexander Murdoch Jr. who founded Murdoch Laboratories, a predecessor of Blackstone Ultrasonics and Blackstone-NEY Ultrasonics. Up until the development of ceramic piezoelectric materials and advanced Langevin type piezoelectric ultrasonic transducers in the mid to late 1960’s the magnetostrictive transducer was, probably, the most reliable and powerful ultrasonic transducer available and was utilized by all ultrasonic manufacturers.
A magnetostrictive ultrasonic transducer consists, essentially, of series of laminations of a magnetostrictively (or ferromagnetically) active material attached directly to a vessel or tank which holds the liquid to be ultrasonically activated. A coil of wire is positioned either around or in proximity to the laminations of magnetostrictive material to provide the oscillating magnetic field required to cause cause them to, in turn, vibrate. The basic construction is shown below.
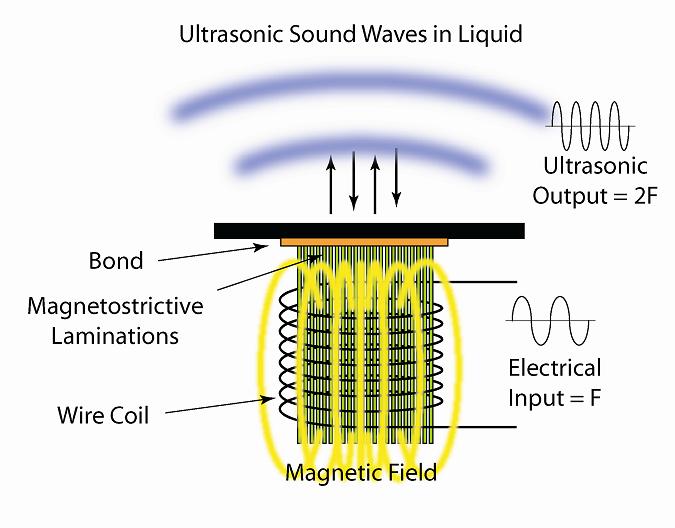
The length of the laminations is such that they are resonant at the desired ultrasonic frequency. Attempts to drive the laminations at a frequency other than their resonant frequency will not result in sufficient amplitude to cause active cavitation of the liquid in the ultrasonic cleaning vessel. The following illustration shows a typical magnetostrictive ultrasonic transducer. Notice that its construction is strikingly similar to that of an electrical transformer with coils wound around a series of laminations.
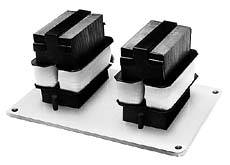
One of the early benefits of magnetostrictive transducers was that the laminations, being of metallic composition, could be metallurgically attached (usually by brazing using silver solder) directly to the ultrasonic cleaning vessel. Piezoelectric transducers, prior to the development of the Langevin transducer design, were not of metallic construction and could only be attached to the ultrasonic cleaning vessel using the adhesive technology available at that time. Since then, adhesive technology has greatly improved and most ultrasonic transducers, including those of magnetostrictive design, rely on today’s advanced adhesive technology for attachment to the ultrasonic cleaning vessel.
Although piezoelectric transducers dominate in the ultrasonic world today, magnetostrictive technology is still available from a limited number of ultrasonic manufacturers and, in fact, is the technology of choice of some users in some applications up to 30 kHz.
– FJF –