The piezoelectric and magnetostrictive effects which drive ultrasonic transducers are capable of creating considerable force but only minimal displacement. In order to produce sound waves of sufficient amplitude (displacement) to cause cavitation in a liquid, some means must be used to increase the displacement produced by the primary piezoelectric or magnetostrictive effect. In both cases, the key to doing this is resonance. As you will remember from preceding blogs, resonance is able to magnify amplitude. A small driving force applied to a resonant device (a bell for example) at the proper frequency will result in a growing vibration of the resonant device at its resonant frequency or a harmonic of the resonant frequency.
In effect, ultrasonic transducers work as acoustic transformers. In an electrical analogy to the acoustic case, the force produced by the vibration source (magnetostrictive or piezoelectric) equates to the current in an electrical circuit while displacement equates to voltage in that circuit. An electrical transformer transforms high current electrical energy at low voltage to lower current electrical energy at a higher voltage.
Note – In the electrical transformer, this conversion can be reversed. In the ultrasonic transducer, however, it can not be reversed as the transformation is due to resonance and not a direct conversion.
Energy is conserved as the overall input energy (as expressed in Watts = Volts multiplied by Amps) is equal to the overall energy delivered at the output. In an ultrasonic transducer, low amplitude, high force displacement is transformed into higher
amplitude displacement with lower force. In both the electrical and acoustic cases, of course, there may be some loss due to other effects in the conversion process but we will discuss these in a later blog.
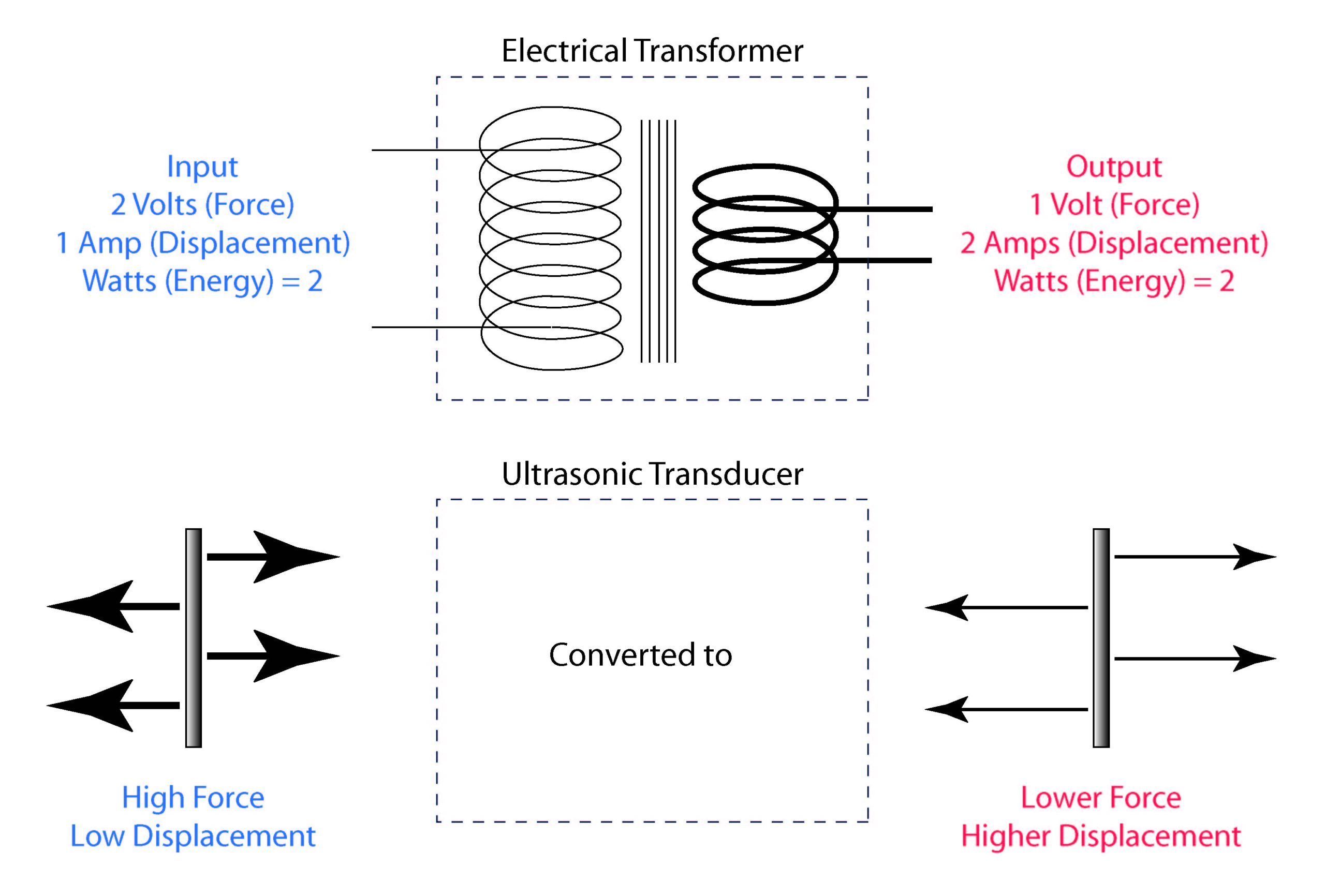
In a magnetostrictive transducer, the vibrating laminations which attach to the ultrasonic tank are cut to a dimension that will make them resonate at the desired ultrasonic frequency. When an alternating electrical current is applied to the driving coil of a magnetostrictive transducer, it produces a pulsing magnetic field which, in turn, results in a small change in dimension of the nearby magnetostrictive material. This small change in dimension is magnified by the resonance of the magnetostrictive material to produce sound waves with the magnitude of displacement required to cavitate liquid within the tank. As the length of the magnetostrictive laminations is decreased, the frequency produced is increased and vice-verse. As the resonant length of the laminations is decreased to increase their resonant frequency, a practical limit is eventually reached when the length of the laminations is too short to accommodate the magnetic field producing coil to be wrapped around it. This practical limit appears to be around 30kHz. I am not aware of any magnetostrictive transducers used for ultrasonic cleaning applications that operate at a frequency much above 30kHz.
In piezoelectric transducers, the piezoelectric driving elements are “sandwiched” between two pieces of metal which along with the piezoelectric driving elements comprise a structure that is resonant at the desired frequency. This arrangement is different from that of the magnetostrictive transducer in that the piezoelectric elements are only a small part of the overall resonant structure and are not, by themselves, resonant at the ultrasonic frequency. This arrangement allows considerable flexibility in transducer design including the ability to operate a single transducer at multiple frequencies by utilizing the harmonics of the overall resonant structure without the constraint of resonance of the piezoelectric driving elements. The piezoelectric elements are used only as a source of vibration to cause the larger structure of the transducer to resonate and need not be resonant on their own merits.
– FJF –