Certain benefits can be derived in ultrasonic cleaning and processing by “pulsing” the ultrasonic generator. In fact, different pulse rates and duty cycles produce different benefits. This blog explores how “pulse” works and how its variants benefit ultrasonic cleaning in different ways.
An earlier blog described the basic function of the ultrasonic generator.
Ultrasonics – Ultrasonic Generator – Introduction
At first, it would seem counter-intuitive that there could be any benefit from turning ultrasonic power off during part of an ultrasonic cleaning process. The blog
Ultrasonics – Ultrasonic Generator – Power Control
in fact, explained that rapidly turning off the ultrasonic generator on and off is one way to reduce total ultrasonic power.
Pulse simply means turning the ultrasonic output of the generator on and off. Two parameters define the generators pulse. The first is the number of times that the power is turned on and off in a given period of time. This is called the pulse rate.
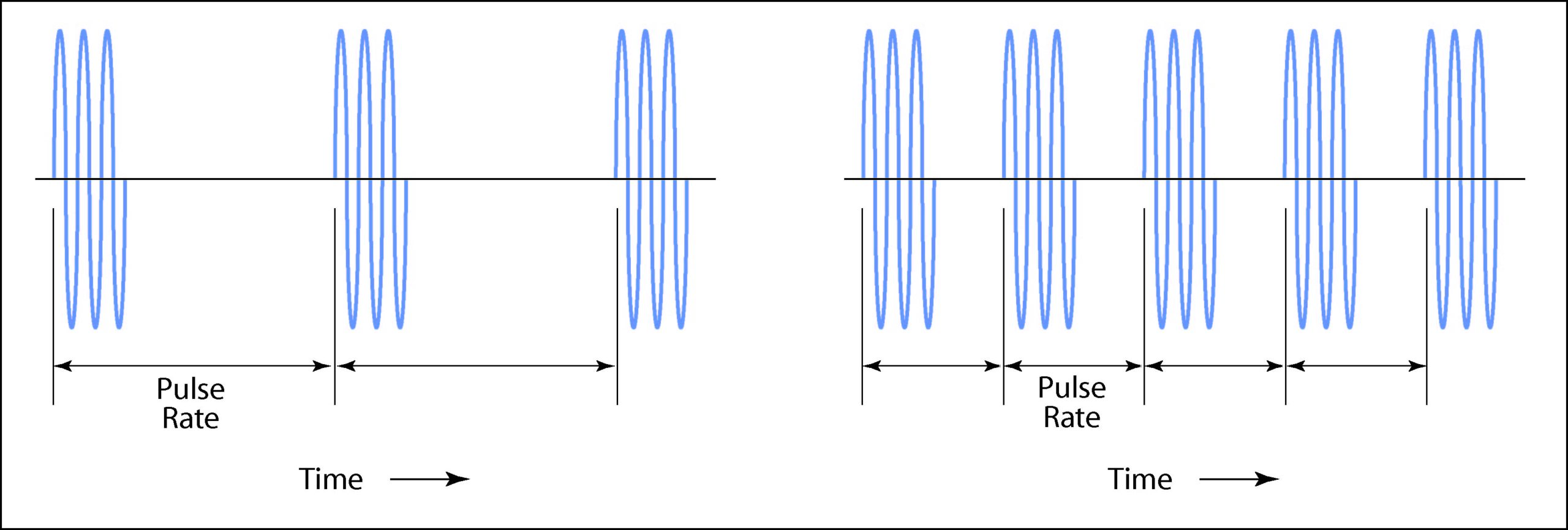
The other parameter of pulse is duty cycle.
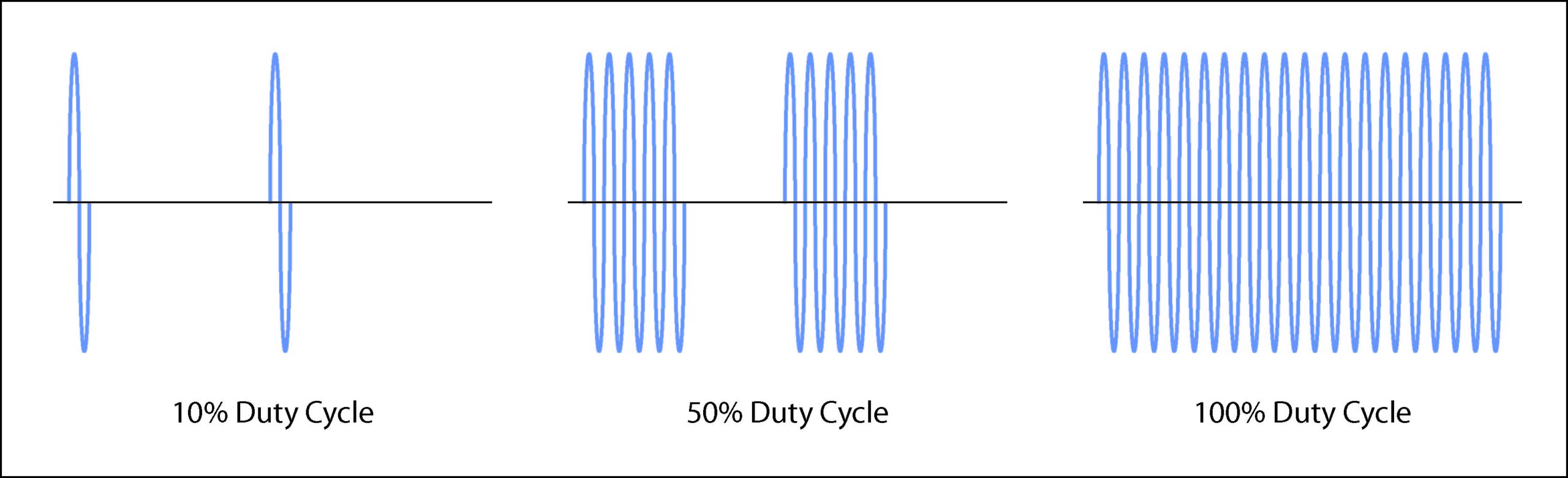
Duty cycle in simple terms is the percentage of time the ultrasonic power is on during each pulse ranging from 0 to 100%.
Historical Note – In the past, most ultrasonic generators had at least a rudimentary form of pulse although it wasn’t necessarily intentional. This unintentional pulse was a result of the fact that very few ultrasonic generators had filtered power supplies which could actually supply a non-varying source of voltage to operate whatever circuit created the ultrasonic frequency output. As the power line varied (due to alternating current) the ultrasonic power varied in amplitude accordingly. Although in come cases the ultrasonic frequency did not totally disappear it at least varied in amplitude at a frequency of, usually, 120 Hz.
In the 1980’s a new breed of ultrasonic generators was developed that was able to intentionally introduce pulse into the ultrasonic output. In basic ultrasonic generators, pulse rate and duty cycle were commonly fixed at values that were considered optimum by a given ultrasonic manufacturer for their particular transducer design. The effect of pulse, in fact, will vary depending on the characteristics of the transducer driven by the ultrasonic generator. More sophisticated ultrasonic generators allowed the user to vary the pulse rate and duty cycle to achieve maximum performance. In general, pulse rates were variable from a few pulses per second up to several tens of pulses per second.
In some cases, a longer pulse cycle called “degas” was provided to speed the degassing of liquids in preparation for ultrasonic cleaning. The degas cycle usually provided a pulse cycle every few seconds and a duty cycle of 10 to 50%. The off time of the degas cycle gave air bubbles formed by ultrasonic cavitation but trapped in the nodes of the ultrasonic wave a chance to float to the surface of the liquid. A video showing this effect will be part of the next blog.
The implosion of cavitation bubbles produced by the ultrasonic waves is, after all, the primary cleaning mechanism at work in ultrasonic cleaning. The more cavitation bubbles that are produced and implode, the better the cleaning effect will be. The introduction of pulse to an ultrasonic cleaning system can significantly improve the cleaning effect by producing more cavitation bubble implosions. This will be described in more detail in an upcoming blog.
– FJF –