Today’s blog continues the discussion of valves as promised starting with manually operated valves. There are three basic types of manual valves – the globe valve, the gate valve and the ball valve. Of course, there are many variations of each but a look at their inner workings will reveal that they all fall into one of the three above classifications. Each type of valve has its benefits and weaknesses which must be considered for a particular application. It should be noted that sometimes a valve’s weakness can be overcome by slightly changing its geometry or inner workings.
The “globe” valve is probably the oldest of manual valves is what most of us have as a “go to” image when someone mentions the word valve. The following illustration of a generic globe valve will help in further discussing its attributes.
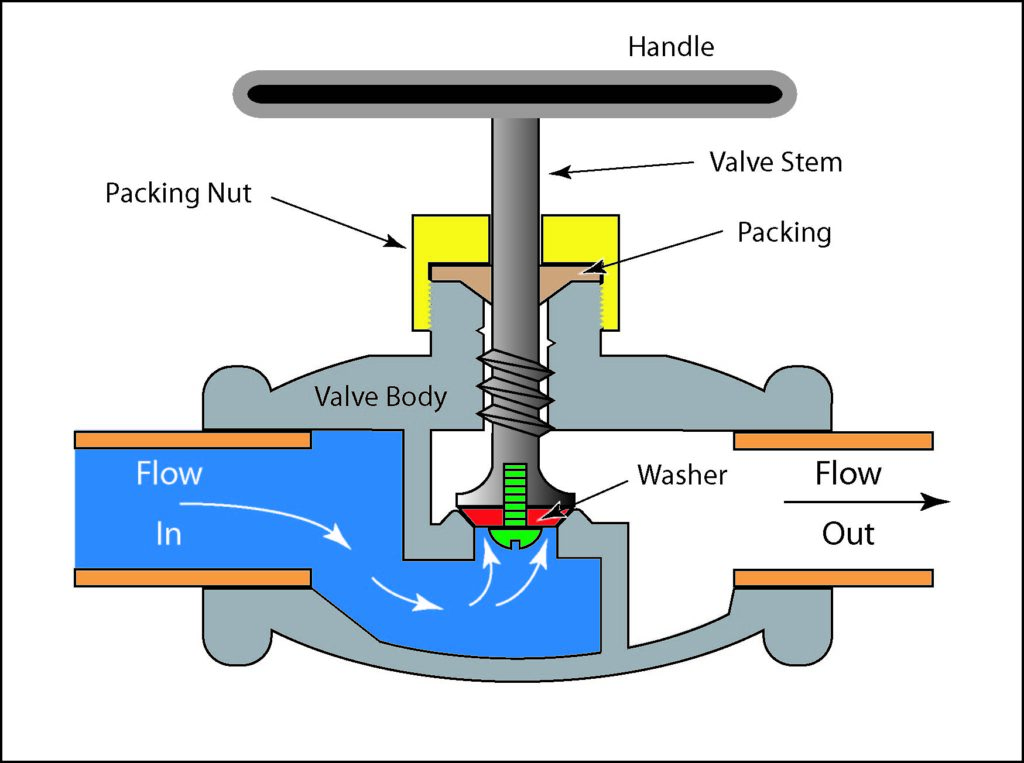
Globe valves are simple on concept, relatively easy and inexpensive to manufacture and are able to handle a wide variety of liquids and gasses. The body of the valve usually starts out as a casting, often a sand casting. Once the casting is poured, the inlet and outlet ports, the valve seat and the packing nut threads are formed. None of these operations requires particularly high precision. The shape of the valve, a “globe,” makes it very strong and able to withstand very high pressures. Globe valves, however, are not particularly good in applications where the valve must be opened and closed frequently. Wear on the washer, which is usually made of a resilient material like rubber, viton or industrial plastics like teflon, eventually results in imperfect seating of the washer against the seat. A worn washer results in a lack a valve’s ability to stop the flow through the valve. As can be seen above, the valve also depends on “packing” to prevent the escape of liquid or gas along the stem of the valve which is not a perfect fit with the body of the valve. Packing leaks will not happen when the valve is closed as in the closed condition, there is no pressure on the outflow side. The Packing, again made of a resilient material, grows old and brittle with time and its seal with the rotating valve stem is usually compromised as a result. The good thing about both of these comparative weaknesses is that both the washer and the packing can be easily replaced. In fact the packing seal can usually be restored by tightening the packing nut.
Useful Tip – Anyone who has turned of the water supply using the valve at the wall under the sink or toilet knows that that valve (usually a simple ball valve) nearly always leaks as you start to shut it off. Fear not – the valve will stop leaking once it is fully closed (the washer pushing against the seat will accomplish this). And when it’s time to turn the valve on again, a simple tightening of the packing nut (under the handle) will re-compress the packing and stop any leaking.
Globe valves, even when they are fully open, provide a significant restriction to the flow through them. The flowing material must round several bends to get through the valve which adds resistance to flow. For this reason, globe valves often need to be sized based on the orifice size (the minimum diameter of the seat) in addition to the pipe size. In short, a valve that fits a certain sized pipe, if it does not have a large enough orifice, may not allow sufficient flow in some applications.
Finally, globe valves are not good at regulating flow. They work best fully open or fully closed and can’t provide a consistently regulated flow when partially open. This is because of the resilience of the washer and the fact that the adjustment of the stem is not designed for precision.
The next blog will discuss another of the three major types of manual valves, the ball valve.
– FJF –