Inadequate or improper agitation of parts in a cleaning tank is a common problem in industrial cleaning. Agitation, if properly applied, can be a very powerful aid to cleaning. The result of improperly applied agitation, however, can range from disappointing to disaster.
The basic reason to agitate a part in a cleaning tank is to provide or encourage a flow of liquid over both the inside and outside surfaces of the part being cleaned. This flow helps flush away contaminants that have been loosened or dissolved by the cleaning chemistry. In the case of parts with internal cavities, proper agitation can serve to exchange contaminated chemistry within the cavity with uncontaminated chemistry so that the cleaning process can continue to completion. Inadequate agitation stroke (distance of movement) can prevent the effectiveness of agitation in this process. The following graphic shows this more clearly than I can describe it in words.
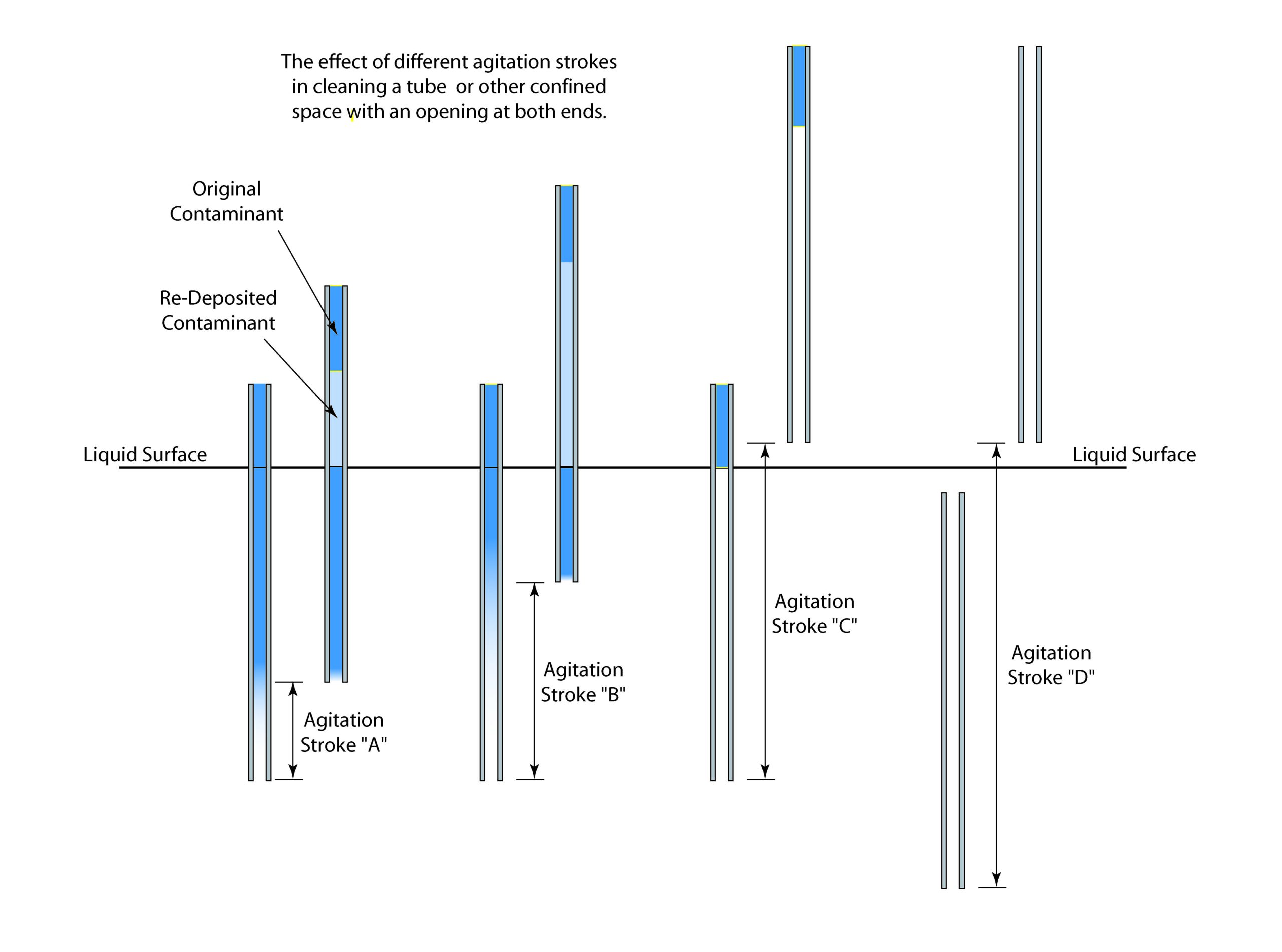
The same problem exists even with a part with a confined space that is open on both ends and is fully immersed. If the agitation stroke is not sufficient to totally displace the liquid within the length of the confined space, a total exchange of liquid within the part will not occur. Theoretically, the immersion stroke of a totally immersed part should be equal to at least 1/2 the total height of the confined portion of the part. More is better!
Finally, if a picture is worth 1,000 words, a video should be worth at least a couple hundred more. In the following video, a glass tube contaminated with food coloring dye is immersed in the laboratory fish tank we’ve discussed before. The effect of increased agitation is obvious.
There are other aspects of agitation other than stroke that can have significant effect on its effectiveness. There are also times when full immersion and withdrawal of a part is not practical. This is especially the case in parts that have a large dimension in the direction of travel for agitation. Some of these issues will be discussed in the next blog.
– FJF –