Pressure regulating valves were discussed in the preceding blog Valves – Pressure Reducing Valves. Pressure reducing valves, although commonly used where pressure is an issue, are not always the best alternative. The pressure reducing valve has a close cousin called a “Back Pressure Regulating Valve” which monitors and controls pressure in a similar but different way. The back pressure regulating valve is actually a better choice in some instances requiring dynamic control of pressure.
The most common example of a back pressure regulating valve for most of us is the pressure relief valve found on hot water tanks in our homes. In this use, the back pressure regulating valve is a safety device to prevent the hot water tank from exploding if it should overheat. Similar valves are used in nearly any situation requiring that pressure not exceed some safe limit. These safety valves are often one operation devices. Once the valve performs its function, it must be replaced.
The following illustration is a schematic representation of a dynamic back pressure regulating valve.
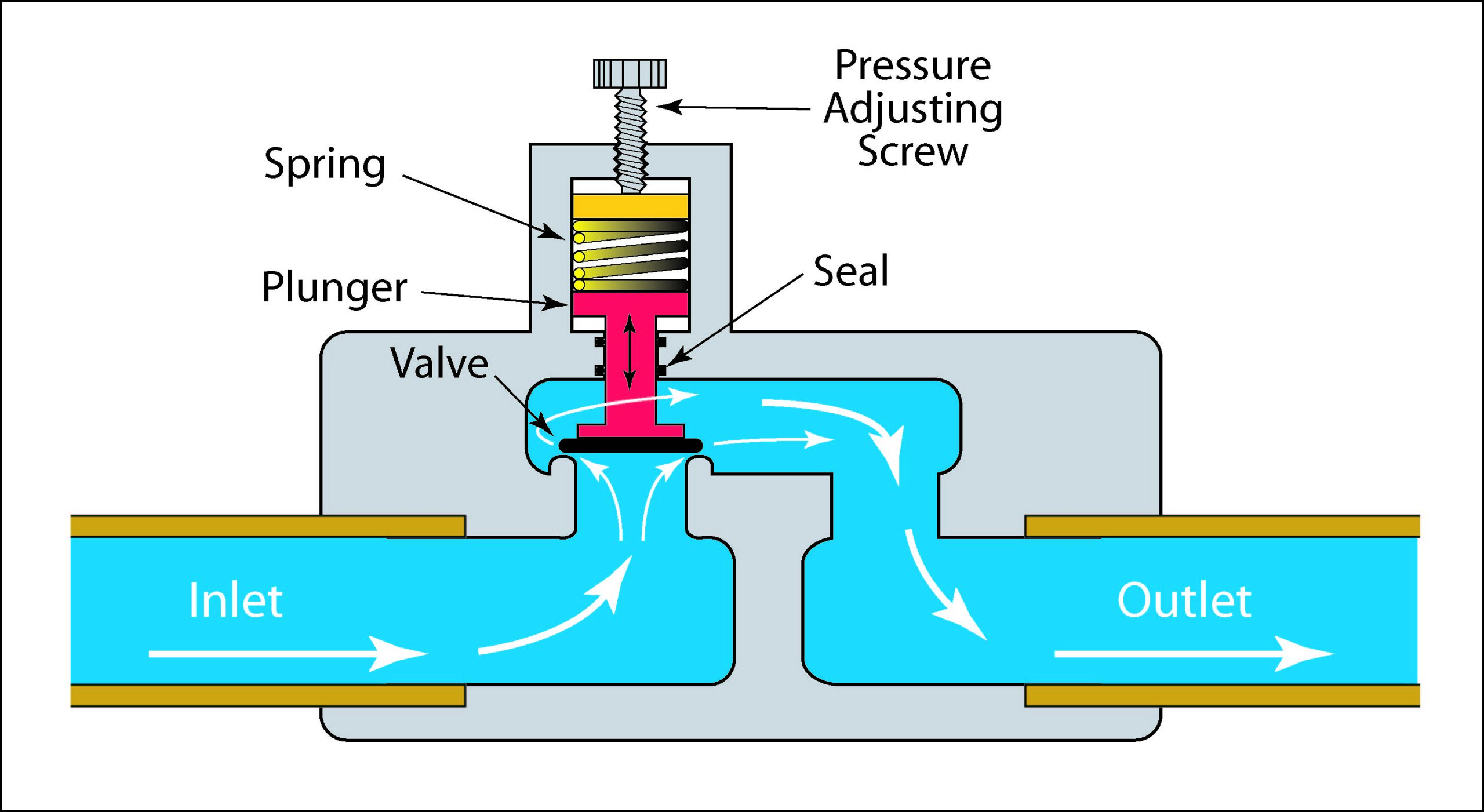
Pressure on the inlet side of the valve pushes against adjustable spring pressure to open the valve once the desired pressure is exceeded. Once the back pressure on the inlet side is reduced, the valve closes to maintain back pressure on the inlet. In order for the valve to function properly, the back pressure on the outlet side of the valve must aways be less than the desired back pressure on the inlet side. If the outlet pressure temporarily exceeds the back pressure on the inlet side, it will be held back by the valve by holding the valve closed. In this case, however, there is nothing to prevent the back pressure on the inlet side from increasing to equal the back pressure on the outlet side.
One more consideration – – In order for this valve to perform its pressure controlling function, it is assumed (and necessary) that increased flow from the source will result in reduced pressure. Although this is a pretty safe assumption in nearly all cases, there may be a few exceptions – so be careful and know the source characteristics when specifying a valve of this type!
This type of valve has some interesting potential that I can’t recall seeing used in typical automated cleaning machines. Consider the following example.
A series of counter-flowing rinse tanks includes a pump and filter which returns filtered liquid from the first tank to the last tank in the series. Meanwhile, one or more tank(s) require an exit spray. The sprays operate intermittently as required. At any given time, none or all of the spray(s) might be activated. Most systems I’ve seen would accomplish this using a pump for the filter loop with automated valves to activate the exit sprays as required. A separate automated valve might be used to turn off the return to the final tank when spraying functions are operational. Another scenario would use a dedicated pump for each exit spray.
The illustration below shows a simpler and likely less expensive solution using a back pressure regulating valve.
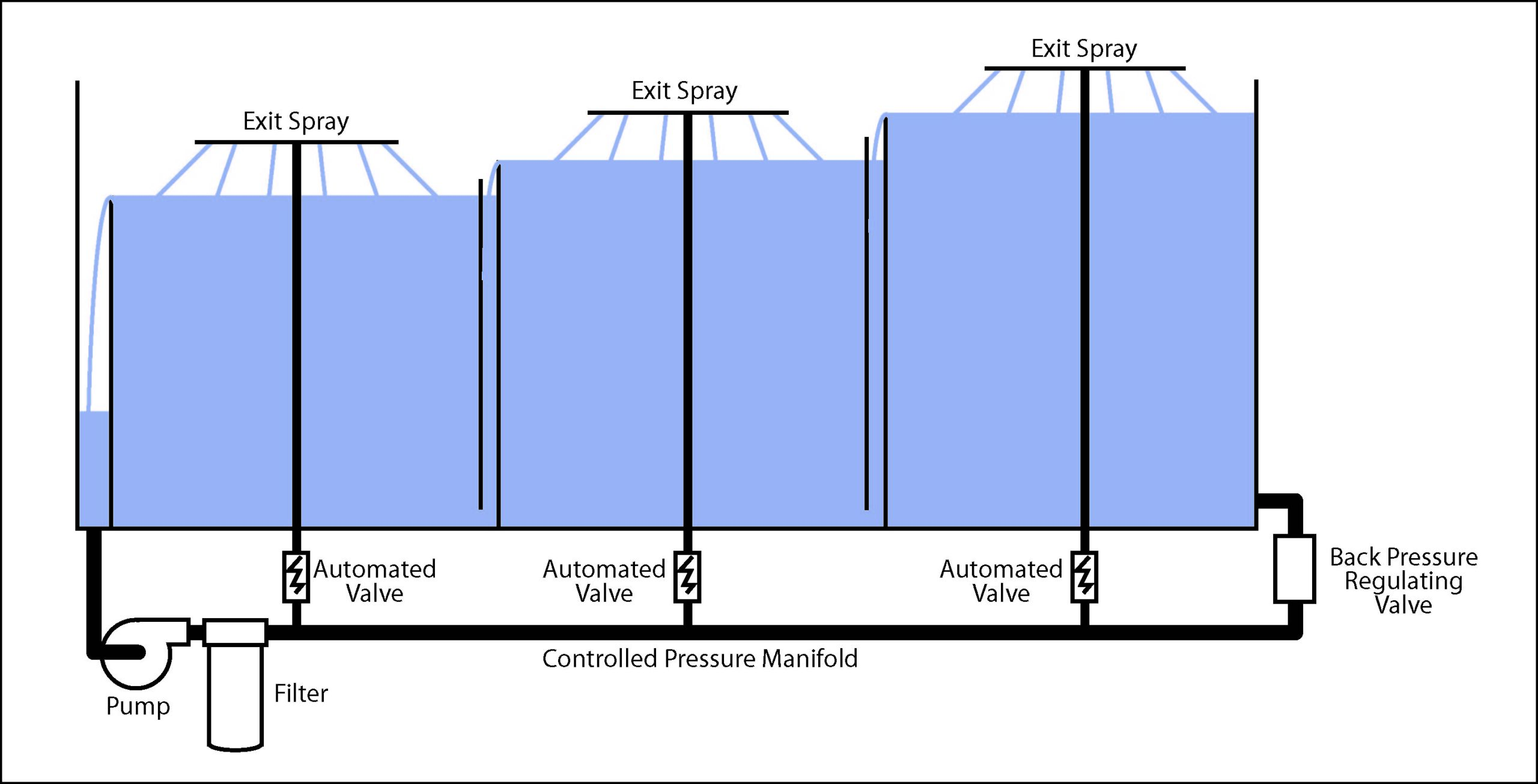
Pressure is maintained in manifold supplying the sprays by the back pressure regulating valve. Depending on the full capacity of the pump and the pipe size of the manifold, all sprays could be used simultaneously with full pressure maintained to all. Excess liquid continues to replenish the rinse tanks. When the sprays are not activated, the full return from the pump is automatically directed to the rinse tank return. An added benefit of this arrangement is that all sprays are supplied with freshly filtered liquid.
I’m sure that all you clever engineers out there can come up with tons more uses for this oft-forgotten, relatively inexpensive and useful valve – the back pressure regulating valve.
– FJF –