For all I have said about drying in the preceding blogs, maybe I should have started with this one. So here we go, better late than never. Although a seemingly “no brainer,” the idea of reducing the load on the dryer by eliminating as much water as possible prior to the drying process itself remains something that is seldom addressed seriously. In a clothes drying analogy, the “spin” cycle of an automatic washing machine considerably reduces the amount of water remaining in the fabric prior to drying. The use of centrifugal force to remove excess water prior to final drying, in fact, can occasionally be applied in parts washing as well. The process, however, can only be applied in situations where part geometry and fixturing considerations favor its use. One of the more common applications is in removing excess water from small bulk hardware items (nuts, bolts, screws, rivets, etc.). Parts are placed in a circular container made of perforated metal and spun to remove excess water. This device may also be called and “extractor.”
So what about the majority of parts where centrifugal extraction is not a practical option? There are some simple things to consider like the positioning of parts so that there will be no “pockets” where water will “puddle.” I’m sure we’ve all learned that water glasses and bowls should be placed in the dishwasher upside down to prevent them from retaining water at the end of the cycle. But, there are also some not-so-obvious things to consider.
To start with, in many cases it is not only the parts that carry water from the rinse to the drying station. Fixtures and baskets may also retain water which must, of course, be removed by drying as well. So, it only makes sense that fixtures and baskets should be designed so as to minimize surface area.
Note – Because baskets and fixtures also consume heat in the drying process it is beneficial to reduce their ability to absorb heat as well. Heat absorption and surface area are related but reduced heat capacity of the basket or fixture material can also play a big role. Smaller and less mass, in general, are good things.
A second, and often equally important consideration is to remove “capillary” spaces which can retain considerable quantities of water. Capillary spaces are small gaps across which water can “bridge” being held in place by the surface tension of the water.
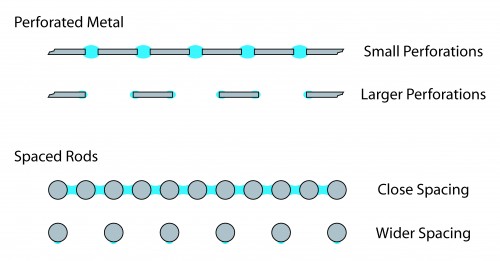
Fixturing should be designed to eliminate closely-spaced components and things like perforated metal with smaller than required perforations. Capillary spaces may be present in the basket or fixturing itself but may also be formed where parts contact the basket or fixture surface. Wherever possible, contact areas should be made as small as possible.
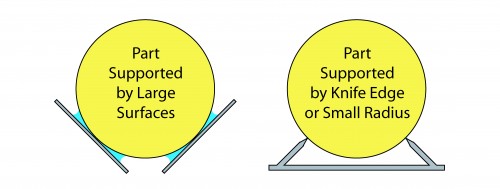
Not only will minimizing contact area between the part and the fixture reduce the water held in the capillary. It will also reduce the likelihood of water spotting due to residues left as the water evaporates. Water spots, of course, are caused as impurities in the water are left behind by the evaporation of the water. Less water means less impurities hence less spotting.
Proper part orientation and basket or fixture design can significantly simplify a drying process. Of course, it is not always possible to have the ideal situation. In the next blog I will reveal some other ways to reduce the load on the final drying process.
– FJF –