The movement of air is an important consideration in the design of most industrial cleaning systems. The immediate application that comes to mind is, of course, in drying. The movement of air is one of the major requirements for drying along with, of course, elevated temperature. In most cases, the need to move air in a controlled way is met using fans of conventional design ranging from ones with simple blades (similar to a ceiling or window fan) to more industrial types with rotating impellers. These are called “squirrel cage” fans or blowers (the name comes from the similarity in appearance of the impeller to the exercise wheel often found in cages for hamsters and other small pet rodents).
Fans are used for drying, cooling electronic devices, exhausting fumes and in a number of other ways in industrial cleaning systems. As useful and varied as fans are, however, they sometimes fall short in meeting a particular need when it comes to the required volume and/or pressure. For drying and cooling, compressed air is often considered as an option. Many applications, however, don’t require the extreme pressure of compressed air. Compressed air is also relatively expensive to produce and introduces the risk of oil contamination as many air compressors use oil to lubricate the compression mechanism.
Regenerative (often shortened to “regen”) or vortex blowers fill the void for applications that require more than a fan but do not require compressed air.
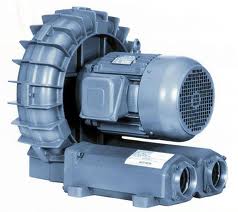
A regenerative blower is comprised of an impeller (similar to that found in a centrifugal pump for moving liquids) rotating inside a shroud and driven by an electric motor. This impeller has a multitude of vanes or compartments around its perimeter. Air from the inlet port enters the compartments nearer to the center of rotation of the impeller. Once the air has entered the compartment, centrifugal forces it outwardly toward the outside of the impeller. The air, now compressed by centrifugal force, is then directed to the base of another compartment by features present in the housing or shroud. The air is then again compressed as it is again forced to a position nearer the outside circumference of the impeller. This action is repeated a number of times as the impeller completes its rotation. Finally, the compressed air is collected by a “stripper” and directed to the outlet of the blower. The following diagram may be helpful in understanding this process.
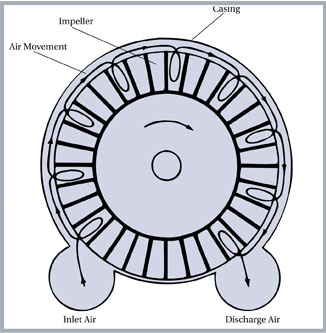
“Regen” blowers are typically used in applications requiring a volume of air in the range of 10 to 1000+ CFM and at a pressure of from .5 to 10 PSI (rough numbers only) and have several potential advantages over conventional fans and compressed air –
- Regen blowers can also be used to provide vacuum and are frequently used for applications including holding parts in fixtures.
- Regen blowers, because of the intense internal friction of the air as it moves through the blower, add considerable heat. The temperature increase as air moves through the blower may be 20°F or more. This heat can be useful for drying.
- Since there are no touching parts (other than the sealed shaft bearing) regen blowers do not cause oil contamination.
- Regen blowers are available that are rated for high temperature.
- Regen blowers are highly efficient.
But, there are some potential problems too – –
- Regen blowers are prone to damage by liquid or solid contaminants being introduced into the inlet. Inlets must be provided with a filter and/or a device to remove water from the incoming stream.
- Regen blowers can be relatively noisy. Housing them in a sound abatement enclosure is not uncommon.
Regenerative blowers, then, are not for every application when it comes to moving air, but are a useful alternative in applications requiring more than a fan but not compressed air.
– FJF –