Just about everyone can recognize the benefits of sterilization to eliminate bio-burden in a plumbing system. Heat or chemicals toxic to living organisms are periodically introduced to kill the offending critters. This process can be conducted using either CIP (Clean In Place) or COP (Clean Out of Place) procedures. CIP simply means cleaning by flushing with heated water, steam and/or chemicals. COP means the disassembly and individual cleaning of all plumbing components. Both are commonly used to satisfy the need for “sanitation.” Clearly, however, these measures are not adequate for the requirements of a “high purity” system. The requirements for a high purity system can only be met by designing plumbing to prevent stagnant areas where particles and other impurities can collect only to be released later with deleterious effect on the process.
A couple of simple examples can be used to illustrate this point – –
Valves –
Nearly all liquid handling systems have at least one valve. At the base level, of course, that valve must be connected using fittings normally considered appropriate for sanitary applications (flange and clamp, orbital welding, etc.). It certainly should not have threaded fittings! Beyond this, things can get a bit tricky. Let’s consider the types of valves we are familiar with from previous blogs – globe valves, ball and piston valves and gate and butterfly valves (sticking with only manual valves for the moment). Of the three, only gate and butterfly valves are suitable for use in high purity applications. Globe valves, because of their internal construction are prone to collecting sediment, especially under low flow conditions. This sediment will remain in the valve even when the system is drained. The construction of the valve, with numerous threads and enclosed spaces is notorious for trapping contaminants. In the case of ball and piston valves, fluid is trapped in the passageway through the rotating or sliding member only to be released next time the valve is actuated. A butterfly valve with its smooth interior surfaces is probably the best choice in high purity applications with a properly designed gate valve ranking second. Again, you have to watch out for those nooks and crannies. When it comes to actuated valves, extreme care must be taken to assure that the chosen valve is suitable for high purity applications.
Pumps –
Let’s look at two more features that are critical in high purity liquid systems and then we’ll move on to other things. As is the case with valves, special attention must also be given to selecting pumps for high purity applications. Although most any style of pump can be rated for sanitary use, additional consideration must be given in high purity applications. A centrifugal pump, for example, can’t really be purged without disassembly. Peristaltic pumps (with a roller squeezing a tube) are inherently as free of impurities as the tube being used but aren’t appropriate in all applications.
Finally, plumbing in a high purity system must be designed so that it can be completely drained as required. This can be as simple as making sure that all piping slopes toward a drain point. However, things like “dead legs” must be considered as well. An example of a “dead leg” is shown below.
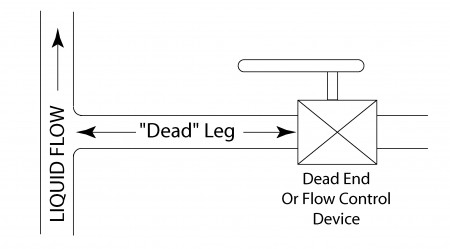
Liquids stagnating in dead leg areas will not be cleared by circulation and/or draining.
So, the things to take away here are that the old term “sanitary plumbing” is often not applicable on “high purity” systems. The use of a specification for “sanitary” plumbing will not assure a system that is suitable for high purity applications. Designers should use common sense in addition to applicable specifications in designing systems for high purity applications.
– FJF –