In the blogs Chemistry – Oil Splitting and Oil Emulsification – Part 1 and Chemistry – Oil Splitting and Oil Emulsification – Part 2, I discussed how oils are removed from parts using chemistry that either splits or emulsifies the oil. The next step is to collect and get rid of or recycle that removed oil. This can be done in a number of ways. In the case of oil that has been split it’s pretty easy. The oil and water (cleaning solution) are in two distinct phases with the oil floating on top of the aqueous based solution. If left on the surface of the cleaning solution in the cleaning tank, however, it would be re-deposited on clean parts as they are removed from the tank and, therefore, must be removed. In some cases, a simple overflow weir and sparger is adequate to do the job.
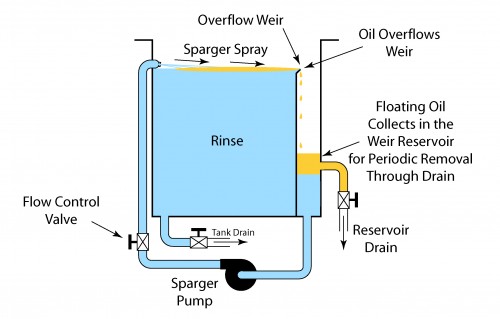
The sparger, though not always necessary, elevates the effectiveness of oil removal using this means.
Oil that has been emulsified or partially emulsified presents a greater challenge. In some cases, the components of an emulsion will separate due to gravity given enough time. This, however, is not likely to happen in a cleaning tank where sprays, turbulation and ultrasonics continually encourage renewed emulsification. Separation and removal of oil in these cases requires using a secondary device called an oil coalescer. An oil coalescer is, basically, a vessel without agitation where oil and water are left undisturbed for a sufficient period of time to allow separation to occur due to gravity. Although this could just be a simple tank that is manually attended, it is preferable in a production situation to have a device that can automate the process.
Most automatic oil coalescer designs are based on the simple principle shown below.
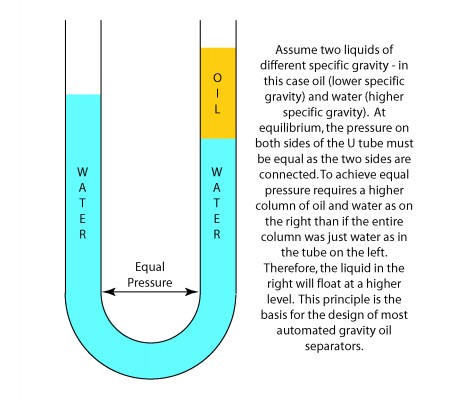
The fact that the oil floats higher provides the ability to direct the oil away from the process. The following illustration schematically shows the construction of a typical oil coalescer used in industrial cleaning.
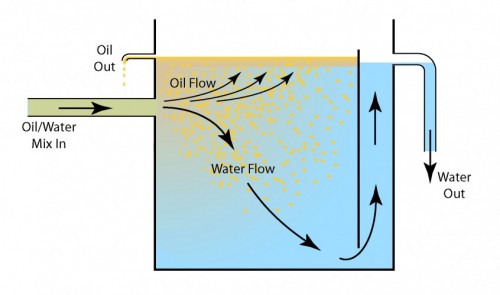
In some instances, baffles consisting of plates or plastic balls (or other shapes) prepared in such a way that oil wants to adhere to them are added to the separation chamber to enhance oil separation. Oil collects on these hydrophobic surfaces until sufficient buoyancy is attained to cause the collected oil to float to the surface.
As with any process, there are some qualifications that must be met for an oil coalescer (or any other means of oil removal) to be effective. I’ll discuss these requirements as well as some other ways in which oil can be removed from a process in the next couple of blogs.
– FJF –