As in nearly any decision making process, one must consider the options available and the pros and cons of each for industrial parts cleaning automation. The next few blogs will describe some of the automation options that are available for industrial parts cleaning along with their benefits and potential shortfalls.
Walking beams and “pushers” have been around for a long time and are relatively simple in concept. They are both implementations of the same basic idea of simultaneously moving a number of racks or baskets of parts from one process step to the next through the use of an indexing system.
Walking Beam –
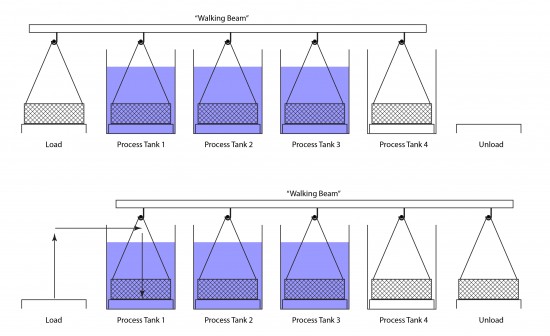
A walking beam is usually positioned above the process path but is offset to the side in some cases. This beam has several hooks that can engage the items to be moved. The beam lifts the items being processed and indexes them to the next process position. Once the items have been moved, the beam dis-engages and returns in preparation for the next indexing event.
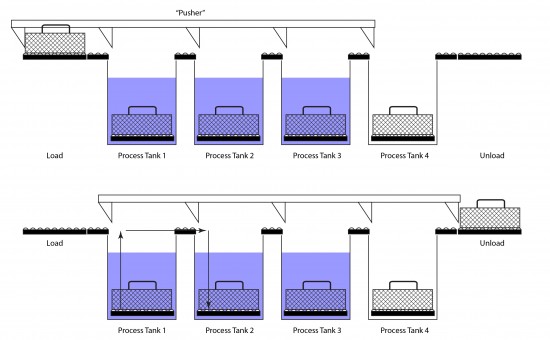
In a pusher system, baskets or fixtures are lifted by a lifting means in each tank to a height above the top of the process tanks. They are then pushed from one process station to the next by a sliding device which engages each basket. Rollers or sliders are usually provided to bridge the gap between process tanks.
There are many variations of walking beam and pusher systems but, in general, any device that indexes baskets or racks from one station to the next simultaneously falls into this category. The benefits and limitations are similar in all cases.
Advantages –
Walking beam and pusher systems are quite simple and are “clockwork” in nature. The same linear motions are repeated each time parts are indexed. They are both very efficient and able to fully utilize process resources as there is a basket or fixture in all tanks except for the short time while the transfer takes place.
Considerations –
I have used the header of “considerations” here as not all of the below are necessarily disadvantages but, rather, are things that must be considered when thinking of a walking beam or pusher system.
Flexibility – Once a system has been installed, the only real variable is the time between indexes. It is not possible, for example, to change the time in each individual process step making it different from the others. The only option is to use duplicate process stations to multiply process times if needed.
Spacing – Because all indexes must be the same distance, spacing between stations must all be the same.
Structure – In the case of the walking beam, the beam must be able to lift the entire weight of all baskets or fixtures at once. The result is that air cylinders or other mechanical drives must be of higher capacity than those of a system that lifts one basket or fixture at a time.
Walking beam and pusher automation systems have served industrial parts cleaning well for decades and continue to be popular in simple applications where processes are well-established and not likely to change over time. In general, they are economical, require little maintenance and are easy to understand and control.
– FJF –