Meaningful temperature measurements depend on the selection of the proper sensors and controls and the proper placement of sensors to accurately measure the targeted temperature. For example, it was previously stated that bimetallic sensors, in most cases, ultimately sense the temperature of air around them. This makes bimetallic sensors a good choice for measuring air temperature in a dryer. To employ them in sensing the temperature of a liquid in a cleaning tank, however, requires that they be placed at a location where the air temperature is directly proportional to that of the temperature of the liquid to be measured. This is not a simple task as heat must be transferred from the liquid through the wall of the vessel containing the liquid and then through the air to the sensor itself. As we have noted before, air (or any gas) is not a good heat conductor. As a result, a temperature measured in this way may either not reflect the actual temperature of the liquid in the tank or may result in a delayed response due to the time required for the heat to be transferred to the sensor through the tank wall and air. Accurate measurements of liquid temperature require that the heat path from the liquid to the sensor be as short as possible giving thermocouples and resistance sensing devices an advantage when it comes to measuring liquid temperatures. Capillary bulb type sensors can be used to measure the temperature of both liquid and air but, in the case of liquid, the capillary bulb itself should be either immersed in the liquid or bonded directly to the wall of the vessel using a suitable mechanical clamp and surrounded by a good conductor such as a highly heat-conductive epoxy.
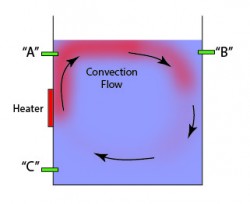
Although selection of the appropriate sensor is critical, even the best sensor will not provide the needed temperature indication if the sensor is not properly positioned. In the case of a tank with heaters mounted on a single side, for example, liquid temperature may vary by tens of degrees depending on the position of the sensor in the tank relative to the placement of the heaters and the depth of the tank. More heaters positioned around the tank will better distribute the heat but even distributed heat will not prevent temperature stratification in a large or deep tank. A better solution is to distribute the heat using a pump loop or propeller type immersion agitator.
It is always a good practice to verify the accuracy of temperature measurements using a reference thermometer. Although most temperature sensors are highly reliable, it is not uncommon for them to become detached or dislocated over time in which case, of course, they are not measuring the targeted temperature. I prefer a laboratory grade mercury bulb thermometer encased in a metal sheath as a reference. Hand-held thermocouple or RTD devices are also useful and especially so in cases where there is no direct access to the area where temperature is to be measured.
Note – Ultrasonic vibrations have been known to have an effect on the accuracy of some temperature sensing devices. To prevent this possibility, reference temperatures should be measured with the ultrasonic energy off in ultrasonic tanks to assure accuracy.
– FJF –