The final type of weir I’ll discuss in this series is the four-sided overflow weir in which liquid overflows all four sides of a process tank.
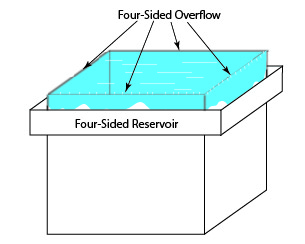
This type of weir is normally found in equipment designed for “precision cleaning” applications and most commonly in rinses where efficient particle removal is a major consideration. The theory behind the benefit of a four-sided overflow is shown in the illustration below.
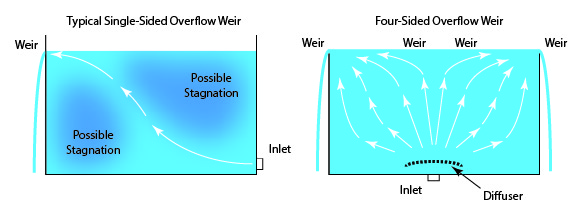
In a tank with a single-sided overflow, liquid usually enters the tank through a fitting located near the bottom of the tank on the side opposite the overflow. In flowing from the inlet to the overflow, the path of the liquid allows for possible stagnation of liquid not in the direct path of flow. Even if the inlet is placed higher on the tank wall or if a sparger is used, the opportunity for stagnation remains and may even become more pronounced, especially near the bottom of the tank. With a four-sided overflow having a diffused inlet at the bottom of the tank, the opportunity for stagnation is significantly reduced. The charts below show the different speeds of recovery of a one-sided over vs. a four-sided overflow.
Logic and evidence supports the benefits of a four-sided overflow. However, successfully executing a four-sided overflow is difficult, especially under low flow conditions (low flow rates are beneficial to ultrasonics and may reduce the use of DI water and/or chemistry). This is because the entire rim of the tank becomes the width of the overflow which is 4 or more times as wide as a single-sided overflow in a similar-sized tank. Four-way leveling also becomes a critical factor. Tanks with four-sided overflow that are part of a multi-tank system should be equipped with a means to level each tank separately once the machine is in place. In addition, the saw-tooth weir design is often used in a four-sided overflow tank to effectively reduce the overflow weir width (especially in larger tank systems) making it easier to maintain flow over all sides of the tank.
– FJF –