De-ionized water is commonly used in both industrial and precision cleaning systems, primarily for rinsing. De-ionized water is a little like the speed of light or absolute zero in that you can never quite TOTALLY remove all the ions from the water (although we can get close) and, once a certain level of de-ionization is achieved, it is hard to maintain or measure (like some of those particles they talk about in quantum physics). In short, de-ionized water is pretty special stuff!
The reasons why we use de-ionized (commonly called DI) water are the exact same reasons why it is so difficult to make and maintain. Water without ions is so “hungry” for ions that it will do almost anything to get them. In many ways it can be compared to a strong acid and, in fact, will attack even the most chemical-resistant materials including the high grade stainless steels commonly used in the construction of cleaning tanks and plumbing. This “hunger” for ions makes it great for rinsing cleaned parts as it will reach into even the most inaccessible places in an attempt to satisfy its ionic hunger by devouring residues from the cleaning process.
Ions are removed from water by passing the water through a column or columns containing resins which strongly attract ions. This process was described in general in a previous blog. Once the ions have been removed, the process of replenishing them starts immediately as the de-ionized water flows through the plumbing lines to the point of use (cleaning system). There is no way to completely stop de-ionized water from re-acquiring ions, but there are ways to reduce the inevitable. One way is to use plumbing materials that minimize the availability of ions. Most plumbing carrying de-ionized water is constructed using grades of plastic that minimize the availability of ions for this reason. Since the re-ionization is also time related, DI water supply systems are often of the recirculating loop design with one or more de-ionizing devices located in the loop as shown in the illustration below.
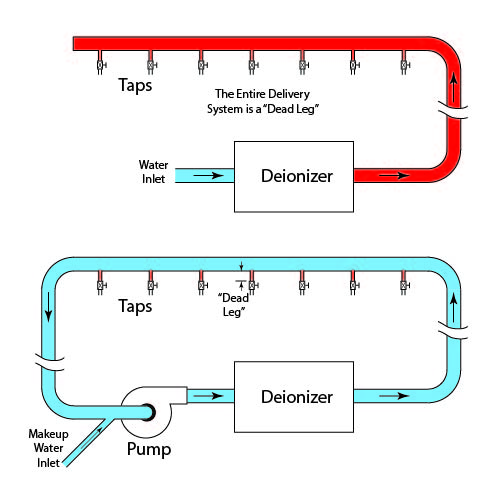
Flow velocities in the recirculating in the loop are typically from 3 to 5 feet per second to minimize the exposure time of the DI water to the plumbing before again being de-ionized.
Note – Another benefit of a re-circulating supply system is that continuous high flow through the de-ionizing beds prevents “channeling” of the beds as described in a previous blog thereby maximizing their life and efficiency.
DI water is supplied through spigots connected directly to the loop with minimum plumbing runs to minimize stagnation. In critical applications, the “loop” may even enter and exit the cleaning system to assure the shortest possible plumbing run to the point of use. Even with these precautions, there are applications which require a final de-ionization unit (usually a mixed-bed resin column) immediately at or following the supply tap.
– FJF –