Adding water to cleaning and rinsing tanks is inevitable in a cleaning process. Most modern machines include a means to sense liquid level and add more water or other appropriate liquid as necessary. It would seem simple enough, but there are a lot of factors to consider in managing liquid makeup.
The first thing to determine is where the cleaning or rinsing solution is going. In general, water is lost in one of two ways, either through evaporation or by being carried out on the parts being cleaned or rinsed. In the case of evaporation, the loss is primarily water as it evaporates leaving chemistry or contaminants behind. In the case of carry-out from a cleaning tank, both water and chemistry are depleted from the tank over time. Of course, in the real world, losses from a cleaning or rinsing tank are usually due to a combination of the above.
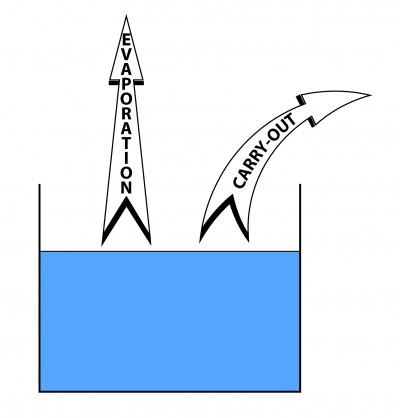
To replace water lost to evaporation, it is only necessary to replace water. A level sensor senses low liquid level and opens a valve allowing fresh water to enter the tank until the proper operating level is achieved. In the case of chemical and water loss due to carry-out, both the water and the chemical component need to be replaced. This can be accomplished by monitoring the chemical concentration using one of the means we have discussed in previous blogs and adding chemistry automatically or manually as needed. Another option is to replenish using a mixture of water and chemistry. This can be accomplished using chemical dispensing devices. The important thing to understand is that the chemical concentration of the replenishing liquid usually doesn’t need to be as high as the target concentration in the tank. This is because part of the losses are probably due to water evaporation. When setting a system of this type, one should consider monitoring chemical concentration over time to determine the proper makeup concentration to maintain the desired chemical concentration in the tank.
If water or water/chemical is added in large quantity there may be other process ramifications. For example, adding a large quantity of cold water may significantly reduce the temperature of the bath. This, of course, could have a detrimental impact on cleaning if the process is temperature dependent. One solution would be to use hot water for makeup. A second consideration in ultrasonic tanks is that the addition of fresh solution that has not been degassed will add entrained gas into the system which may have a detrimental effect on ultrasonic cavitation. For these reasons, level controls should be adjusted so that any one addition of makeup liquid is as small as practical and doesn’t exceed 2 to 5% of the overall tank capacity. In a case where a large amount of makeup solution is necessary, such as when a tank is drained and re-filled, production should be halted until the solution temperature recovers and, in the case of an ultrasonic tank, the solution has been fully degassed.
Finally, in the case of overflow rinses where water is being added continuously, flows should be limited to the minimum that will give the desired result. Heaters should be sized to assure that liquid temperature is maintained at the highest anticipated flow rate.
– FJF –