In ultrasonic cleaners, sound waves (vibration) originating from ultrasonic transducers must be efficiently transmitted into the cleaning liquid where they create cavitation bubbles which implode to enhance cleaning. The weak links in the path from the transducer to the cavitating liquid are typically the locations or “interfaces” where vibrations must be transmitted from one vibrating member to the next. A typical ultrasonic transducer has several such transitions. Maximizing energy transfer within the transducer falls into the realm of transducer design and is under control of the ultrasonic manufacturer. Once the energy is coupled to the vibrating transducer surface, however, there are two remaining transitions which are under the control of the process engineer and become variables in the cleaning process. The first is the transmission of vibration from the transducer output face into the process liquid. The second is the coupling to the contaminant to be removed either by physical displacement or chemical interaction. Our discussion here will address the transmission of sound from the transducer face into the cleaning liquid.
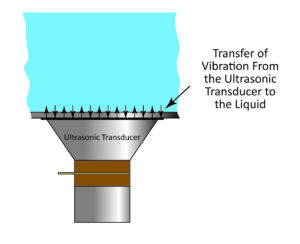
Just as in the case of heat and electricity, there is a limit to the amount of vibration energy that can be passed from one vibrating surface to another. In part, this limit is established by the contact area of the two surfaces (more contact surface allows more transfer just as in heat and electricity) but there are other considerations as well. Specifically, wetting and the tensile strength of the liquid which correspond to conductivity in the worlds of heat and electricity. Assuming that the tensile strength of the liquid will only be exceeded at the point of the formation of a cavitation bubble, this blog will address wetting as a primary limiting factor in the transmission of ultrasonic energy into a liquid.
Wetting –
I have talked about wetting in a previous blog. In order for vibration energy to be transmitted from one vibrating body to another, the two must be in intimate contact. In some cases this is achieved using pressure created by a bolt, clamp or other means as in the case of the elements of the ultrasonic transducer. But in the case of the contact of liquid with the vibrating transducer, there is no such means available. The only “pressure” is that provided by the weight of the liquid. To keep the two in contact, the liquid must “wet” or “couple” the vibrating surface of the transducer. In order for this to happen, the vibrating transducer surface must be wettable by the liquid. In short, there must be an attraction between the liquid and the vibrating transducer. If the cleaning liquid is water-based, the transducer surface must be hydrophilic. Anything about the transducer surface that prevents good wetting by the cleaning liquid will result in reduced transmission of energy. Oil, grease, paraffin, and coatings including Teflon, plastic and other hydrophobic materials drastically reduce the amount of energy that can be transmitted from a transducer into the cleaning liquid. Accumulated contaminants on the tank bottom will also reduce effective energy transfer. On the liquid side, wetting is improved by adding wetting agents to the cleaning chemistry. This explains why de-ionized water (which does not have added wetting agents) is difficult to cavitate and explains why cleaning chemistries that work well with ultrasonics usually have high concentrations of wetting agents as part of their formulation. High vapor pressure and elevated temperature also reduce energy transfer efficiency.
When the liquid does not wet the transducer surface, or when the acceleration due to the amplitude of vibration exceeds the strength of the wetting
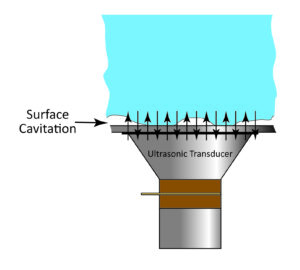
bond between the transducer and the liquid, the two separate or de-couple. This phenomenon is frequently referred to as “surface cavitation.”
In essence, cavitation occurs at the surface of the transducer. This not only reduces the amount of vibration energy that can be transferred into the bulk of the liquid but also has a detrimental effect on the surface of the transducer which results in accelerated erosion or pitting of the transducer surface due to surface cavitation. Although surface cavitation is unavoidable in the long run, providing the best wetting conditions possible will significantly slow its progression.
Enhanced wetting is only one way to improve the transfer of ultrasonic energy into a liquid and minimize surface cavitation. Other considerations will be discussed in an upcoming blog.
– FJF –