The notion persists that more power is better in ultrasonic cleaning applications. In the past, this may have been an absolute as the amount of power available was often limited by the limitations of the equipment that was available. As we discussed in a recent blog however, today’s ultrasonic equipment is no longer limited in power by the existing technology as it was in the past, at least from the standpoint of the ultrasonic generator.
Note – In recent years, the output capability of ultrasonic generators has begun to challenge the ability of available ultrasonic transducer hardware to accept and transmit the available power into the cleaning liquid. This was discussed in the blog More Isn’t Always Better.
It is now quite possible to provide too much ultrasonic power with results that are not beneficial to cleaning and, in fact, may be detrimental not only to cleaning but to equipment life as well.
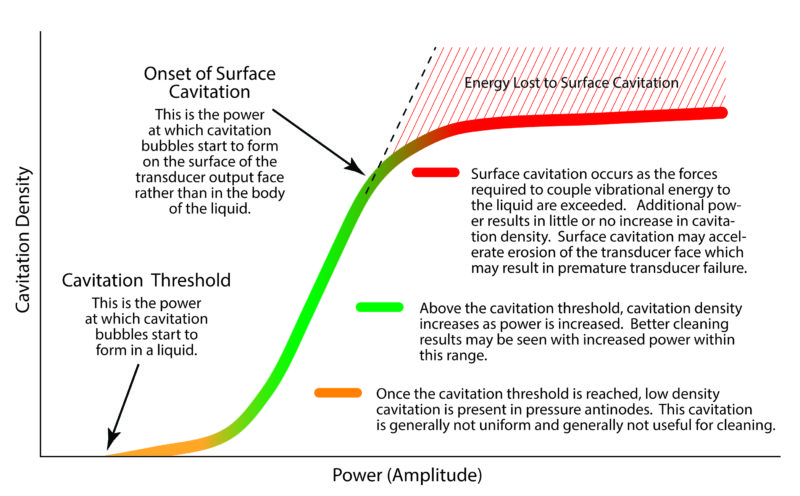
Creating cavitation in a liquid requires a certain amount of ultrasonic energy. The minimum amount of energy required defines the threshold of cavitation. At very low power, cavitation occurs only in anti-nodal regions of the ultrasonic wave and results in limited and non-uniform cavitation bubble density. Such extremely low power is not favorable for ultrasonic cleaning. As power is increased, cavitation density increases until cavitation fills the entire volume of the liquid in an ultrasonic cleaning tank. The addition of even more power results in more and more cavitation density as evidenced by more and more cavitation bubbles forming in the liquid. It is in this power range that increased power may provide better and faster cleaning. There is a power level, however, at which the transducer is no longer able to transmit more vibrational energy into the liquid. Essentially, the transducer face is moving so rapidly and with such amplitude and acceleration that contact between the transducer and the liquid is lost.
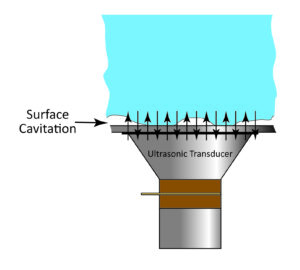
When this happens, the cavitation density in the region not immediately adjacent to the ultrasonic transducer may be reduced. In effect, the bubbles forming at the transducer/liquid interface provide a barrier for the transmission of vibration into the rest of the liquid. In addition, the intense cavitation at the transducer/liquid interface results in an increased likelihood of cavitation erosion of the transducer surface which may lead to premature failure of the transducer. There is more information on this at the blog Ultrasonics – Surface Cavitation Erosion.
In a perfect world, it would be nice to be able to assign specific values to the chart above so that it could be used as a guide to avoid the surface cavitation effect. Unfortunately, this is not possible due to the fact that there are so many parameters involved that can have a significant effect. These include but are not limited to the following –
- Temperature
- Chemistry
- Wave Form
- Tank Size and Shape
- Transducer Type
- Transducer Spacing and Placement
- Work Load
The “take away” here is that there is the possibility of having too much ultrasonic power in an ultrasonic cleaning system. Also that excessive power may result in poor ultrasonic cleaning and accelerated deterioration of ultrasonic equipment.
– FJF –