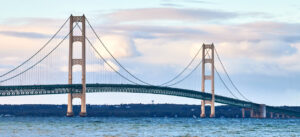
The applications for wire seem limitless. Wire is used for electrical conductors as well as in structural applications including suspension bridges and other architectural creations. There are about 1 ½ miles of wire in a typical car today and often over 150 miles in a jetliner. A cruise ship? Somewhere around 3,000 miles! Wire diameters range from microns to, in the case of multiple stranded cables, several inches to several feet.
Most wire is produced by starting with a rod of metal which is pulled through a series of progressively smaller dies until the desired diameter is achieved. In the drawing process, lubricants are applied to reduce friction. Lubricants, oxides and other contaminants become imbedded in the surface of the wire due to the pressure and abrasion of the drawing process. Because of this, wire presents a consistently difficult cleaning challenge.
Overview –
Wire is typically handled in rolls for ease of transport and storage. However, because of the tenacity of the contaminants, wire cleaning usually requires a combination of chemistry and a direct application of mechanical energy to the wire surface in the form of brushing, wiping and/or ultrasonics. This is not possible if the wire is in a rolled configuration. Instead, most critical wire cleaning is accomplished using reel to reel machines in which the wire travels through the cleaning process in a straight line or over idler pulleys. The idler pulley concept saves space but also subjects the wire to bending and abrasion as it travels over the idlers and is inherently difficult to “thread.” A straight line machine is ideal from a standpoint of ease of threading, minimum bending and the prevention of additional contamination.
Challenge –
This study is of two applications requiring precision cleaning of wire in large quantity. In one case, the requirement was to clean Titanium alloy wire being supplied for a medical application. Obviously, the cleanliness of the wire in medical is of utmost importance. Another case required cleaning a hardened steel alloy wire prior to its being electron beam welded to the edge of a steel strip and ultimately sharpened to create a durable saw blade. Through laboratory testing, it was shown that the required cleanliness in both cases could be achieved using high intensity ultrasonics with a mildly alkaline chemistry. However, even with ultrasonics, cleaning required an exposure time of approximately 5 seconds and needed to be followed by an ultrasonic rinse and air drying. Based on the required production rate, it was determined that a machine nearly 100 feet in length would be needed to provide the required exposure time based on cleaning the wire a single strand at a time at the required speed. Space and budget limitations dictated that a different approach be found. It was felt that a machine capable of cleaning multiple strands of wire simultaneously would be the best solution. Equipment could not be found that was capable of delivering a high intensity ultrasonic field to as many as 20 strands of wire simultaneously. The existing high intensity devices operated on the principle of surrounding the wire with a radial ultrasonic transducer and had a limited working envelope.
Solution –
To solve this problem, Blackstone-NEY Ultrasonics engineers utilized the concept of “constructive interference” of ultrasonic sound waves. High power immersible ultrasonic transducers were positioned to produce a “standing wave” at a location ¼ wavelength below the liquid surface. The wire travels through this high intensity zone
Process –
Using this approach, it was possible to process many parallel strands of wire simultaneously. As an added benefit, top access allowed easy threading of the machine even while other wires were being actively processed. Wires pass through slots in the ends of a series of flooded, open-topped process chambers which ultrasonically clean, and rinse them. A constant re-circulation of liquid precisely maintains the level in the process chambers despite the fact that liquid is constantly being expelled through the slots in the ends of the chambers. The final step is a compressed air blow-off dry.
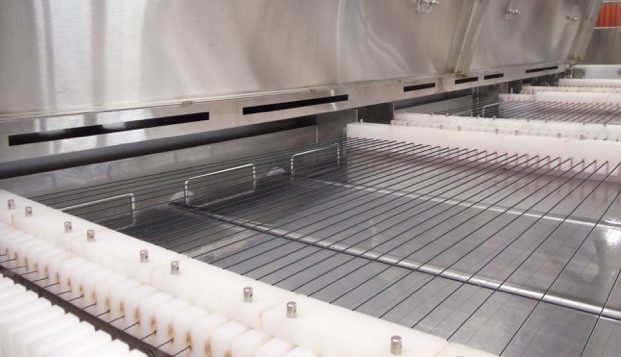
Cleanliness Evaluation –
Due to the difficulty of applying many of the typical cleanliness test methodologies to a thin strand of wire, the “white glove” test predominates as a common means of determining wire cleanliness along with microscopic examination. Passive means such as Millipore® testing often fail to reveal tightly adhered but critical contaminants that result from the wire drawing process. The white glove test is quick and easy and is sensitive to these contaminants.
Click here for a link to a downloadable PDF of this case study