A few years ago I wrote a post about the possible perils of automated valves. The thrust of the post was that many automated valves rely on significant line pressure to hold the valve tightly closed. In applications where there is only gravity pressure, as in drain lines for example, valves that are perfectly effective under high pressure situations may leak like sieves if there is little or no pressure to assist in their function.
A recent experience leads me to re-visit this issue but this time the subject is check valves.
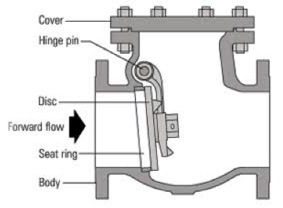
A check valve is a device that allows liquid to flow through a pipe in only one direction. It is really much like an automated valve but with no actuator – – the flowing liquid is the actuator. Think of it as a door that only opens in one direction. If you push from the wrong side, it won’t open. When the liquid tries to flow in the wrong direction, the “door” of the valve slams shut. Although in some cases the check valve has a spring to encourage the door to close when there is no liquid flow, the spring acts as a door closer on a screen door but unlike the typical screen door, there is no latch to hold the valve firmly shut. Holding it firmly shut is left to the pressure it is resisting. If there is no pressure to latch it shut, the door “rattles” and can allow liquid to pass. Contrary to intuitive reasoning, the check valve is often more effective under high pressure than it is under low pressure and may, indeed, need a certain pressure differential to operate at all. The consequence of this is that when check valves are installed to maintain liquid levels in process tanks, there may be an unexpected back flow of liquid over long periods of time as gravity and siphon work to equalize liquid levels in connected tanks or reservoirs. Selection of check valves for low pressure applications is tricky especially if there is very little forward pressure to work with in the first place. If, for example, a valve is chosen that has a spring to hold it closed, the strength of the spring must not be sufficient to resist flow in the desired direction.
The variety of operating schemes in check valves is very broad. As a result, not every check valve will function properly in just any application. Every application should be given more than casual consideration. The operation of check valves is critically important. Important things to consider are
- The back pressure that is required to hold the valve securely closed and prevent backflow. This can range from zero to several 10’s of psi.
- Does the valve seat tightly and remain securely closed under a low or no flow or pressure differential situation? This depends on the type and design of the seat and the closure mechanism.
- The pressure that is required to open the valve and allow flow from a closed condition. Again, a wide pressure range here.
- Valve orientation. Many check valves are designed to be used in a specific orientation and may function unreliably or not at all in a different orientation. Plumbers and assembly technicians should seek and heed the manufacturer’s specifications for installation.
Although the concept is simple, the proper selection and installation of a check valve is not. Don’t consider it a trivial matter.
– FJF –