When particles are the enemy, my general rule is filter, filter, filter! The cost of filtration is small compared to the overall benefit even if it is only “insurance.” There is, of course, the initial cost of installation (filter housings, pumps, plumbing, etc.) but the cost after that is going to be pretty much fixed provided that the condition of the filters is monitored and they are not changed needlessly. There is, after all, just so much stuff to filter out. Most of the comments that follow are directed at the filtration of liquids but may also apply to air or other gasses as in a clean room – but that’s another blog.
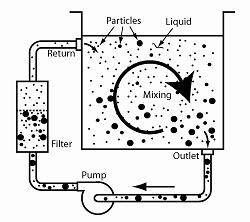
Filtration is commonly applied in a re-circulation loop. Liquid is re-circulated repeatedly through a filter and returned to the source. The technique described here is usually applied in cleaning tanks where particles are being removed from parts being processed.
The blog Sorting Out Filters – About Re-Circulation discusses this concept of filtration. In this case, it is all about turnover and mixing.
Turnover – The number of times a tank would be refilled in a given period of time (usually an hour) at the recirculation rate of flow. For example, a re-circulation loop with a pump rated at 8 gallons per minute returning to a tank with a total volume of 80 gallons would provide 10 “turnovers” per hour. Obviously, turnover can be increased by increasing the flow rate through the use of a higher capacity pump. But turnover can also be increased by reducing the volume of liquid being filtered while using the same pumping capacity. This reasoning countermands the intuitive use of larger liquid volumes (larger tanks) to provide increased dilution of contaminants. A smaller liquid volume will be refreshed more quickly and thoroughly than a smaller one at a given flow rate. This is because the number of turnovers is higher
Mixing – As filtered liquid returns to the source volume, it mixes with the remaining liquid to reduce the overall particle population. Anything that can be done to improve the efficiency of mixing of the filtered return liquid with the source liquid will speed the overall efficiency of the particle removal process. Inefficient mixing may result in areas of stagnation where particles collect. Although it’s not always possible to provide aggressive mixing as with stirring device, other methods such as careful arrangement of filter returns to encourage mixing may be effective.
Pushing It Further – The chart in the above blog assumes that mixing is thorough and instantaneous. In reality, the curves are probably a bit optimistic because thorough and instantaneous mixing is not a reality in most cases. However, the curves can be shifted more to the left if mixing is altered in preference of more particle laden liquid returning to the filter. One way to do this is using cascading rinse tanks as shown below.
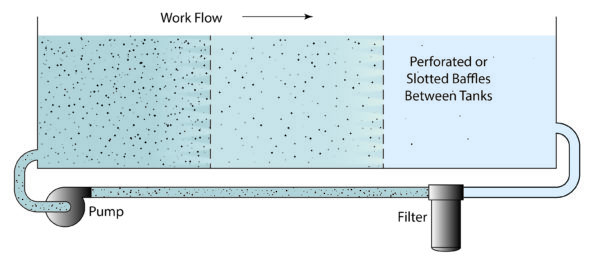
Using two, three or more tanks in series as shown greatly improves the cleanliness of the final of the multiple rinses using the same liquid flow rate. Although generally applied in cleaning tanks, this same concept can be utilized in rinses when water is at a premium.
Quick Dump – In the extreme, the tank may be totally drained and then refilled with freshly filtered liquid one or more times during the cleaning cycle. The incoming liquid could be fresh or retrieved from a reservoir capable of holding the entire volume of liquid exiting the process tank. In some industries this is referred to as a “quick dump rinse.” It can provide a totally filtered tank of liquid for each batch of product processed if necessary.