Successful ultrasonic cleaning processes utilize a combination of mechanical action provided by the formation and implosion of cavitation bubbles and chemistry that dissolves and/or promotes the wetting and transfer of mechanical energy to dislodge the contaminants to be removed. The interactions and effects of chemistry on the ultrasonic process obviously exist but are not well defined. In short, there are chemistries that just don’t work well with ultrasonics for reasons often not understood. The best explanation for this is chemical properties which interfere with the formation and implosion of cavitation bubbles.
There are several well documented associations between properties of chemistry and ultrasonic performance. Reducing the surface tension of a chemistry, for example, is known to enhance the ultrasonic effect. Similarly, there is a perceived benefit to reducing the tensile strength of the cleaning liquid within a certain range. The benefit of higher temperature, another important variable, is probably due to the enhanced chemical effect as well as moving physical properties of the liquid in a direction favorable for ultrasonics. But, it has also been demonstrated that as temperatures approach to boiling point, there is a reduced mechanical effect due to reduced implosion intensity as the vapor pressure of the liquid approaches atmospheric pressure – another physical effect. Chemistries formulated using largely builders, surfactants and many other common ingredients perform in a way that is generally predictable. But there are those formulations that bring cause for question. Again, as with so many things in ultrasonic technology, the following is a collection of anecdotal observations and speculation that may not be supported by current science.
Emulsions –
Emulsions are forced mixtures of two liquids (in the case of cleaning chemistry one usually being water) that are promoted and sustained through the use of a surfactant. Emulsions can enhance the effectiveness of a cleaning chemistry as the chemical attributes of multiple ingredients can be combined. Emulsions may also be formed when contaminants are emulsified in the process of their removal in cleaning. In fact, however, the components of an emulsion do not actually mix but exist together through the power of the surfactant micelles which are molecules with one end that is water-loving (hydrophilic) and the other more attracted to the other emulsified liquid (hydrophobic). The strength of attraction or tensile strength of the bonds with the micelles is, in most cases, not as powerful as the bonds within the liquids themselves thereby reducing the overall tensile strength of the mixture. Reduced tensile strength may result in the formation of too many cavitation bubbles each of which are smaller in size due to the overall distribution of energy and implode releasing less energy.
Cosolvents –
There are a number of solvents that are miscible with water. Miscible simply means that they form a homogenious mixture in any proportion with water. Ethyl alcohol and Butyl Glycol (one of the ingredients in and the source of the distinctive smell of the popular window cleaning product Windex) are common examples of cosolvents.
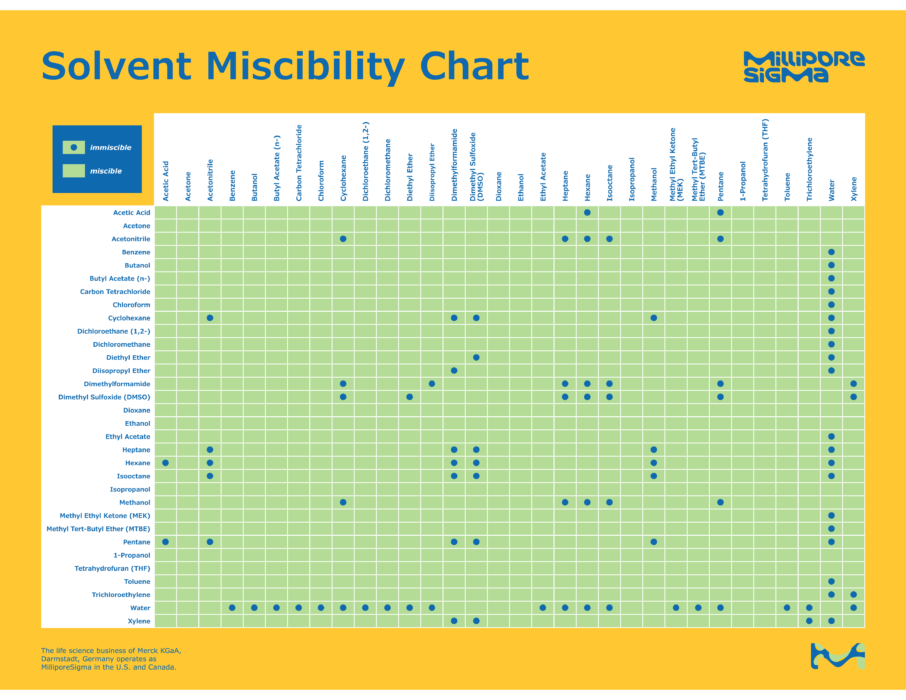
As one can see from the above, there are a limited number of cosolvents that are directly miscible with water. It is, however, it is often possible to force cosolvency of otherwise immiscible solvents using a third co-miscible solvent that is miscible with both. The use of cosolvents is attractive to elevate solvency to a level higher than plain water. Many of these cosolvents, however, have a considerably higher vapor pressure than water. Higher vapor pressure can interfere with the implosion of cavitation bubbles as bubbles fill with vapor which cushions implosion.
Defoamers –
Many chemistries are formulated to minimize the formation of foam (suds). This is important especially in the case of chemistry intended for use in spray washers where excessive foam formation is problematical for obvious reasons. Several mechanisms are utilized to reduce the formation of foam but, despite the mechanism, the goal is to prevent the formation or sustainability of bubbles. The formation of bubbles, of course, is the first and a mandatory stage in a cavitation event. Preventing the formation of bubbles or reducing their stability (at least until they grow to sufficient size to violently implode) can’t be good for the ultrasonic process.
Conclusion –
All of the above are anecdotal and largely not supported by rigorous scientific investigation but does give cause for thought. The majority of chemical formulators concentrate on chemical effects for performance enhancements giving little or no consideration to maximizing ultrasonic performance as part of the process. In my estimation, there is significant enough correlation seen in anecdotal observations to support additional effort on the part of chemical formulators to explore ultrasonic performance effects as well as the chemical effects in the development of chemistry for ultrasonic applications.
JF