Liquid level sensors are used to indicate liquid level by sensing the presence of a liquid using several different means. The “float” type sensor is the one that probably comes to mind first for most of us. The float valve in a toilet tank is a prime example. In the case of the toilet, a float attached to a lever mechanically operates a valve to initiate the flow of water as the tank empties then stops water flow once the required level is met for the next flush. Although direct mechanical control is an option, in industrial applications, the movement of a small float is often used to activate a switch that provides an electrical signal to an indicator or a solenoid valve to control liquid flow. These devices are called float switches.
Two common types of float switches are shown in the illustrations.
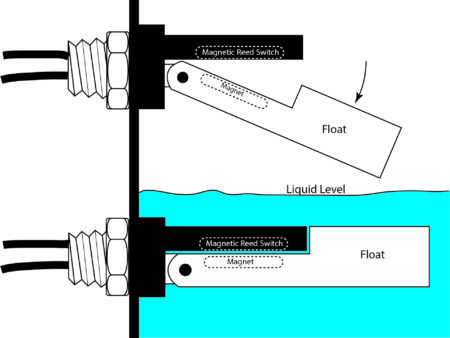
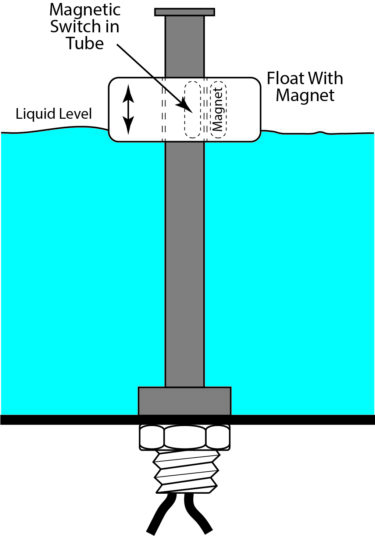
Float switches are simple, economical and work well in many applications. Unlike some other types of liquid level sensors, they are not sensitive to the conductivity, temperature or specific gravity of the liquid they are sensing and can be fabricated using a number of different materials to be compatible with most liquids. They are easy to understand, troubleshoot and replace making them particularly “user friendly.” Float valves are probably the most commonly used device to detect liquid level.
They are not, however, the ultimate answer to every liquid level sensing need. Because float switches have moving parts, they are subject to wear and a variety of mechanical failure modes. For example, a well-designed float valve may be reliable when used with plain water. But if the water contains chemicals which may cause a deposit on the working parts of the sensor over time its reliability is subject to question. They can get “stuck.” This is especially troublesome in the case of a float valve sensing high level which gets repeatedly wet and dry allowing deposits to collect and solidify building up a crusty residue. Particle contamination is also an issue. Chips and even clumps of magnetic particles can be attracted to the magnets and interfere with the magnetic activation of the reed switch. In some cases, the magnetic switch is replaced with a different kind of switch that senses the angle of the float using mercury to bridge contacts in a sealed tube when a particular angle is achieved. This approach, however, is troubled with making reliable contact to the moving switch housed in the float which must, of course, move up and down. When using float type level sensors, it is recommended that they be protected using a small cage or baffle due to their susceptibility to incidental mechanical damage.
One variation of the float switch is a sealed housing containing an angle sensitive switch much like the mercury switch described above. In this case, the sensor is tethered in the vessel in such a way that it floats on the liquid surface on it’s side until the critical liquid level is reached. When this happens, the sensor is pulled to an upright orientation by the tether which then activates the switch. This type of float switch is used primarily in tanks used for liquid storage. It finds little application in the cleaning industry because of the interference it would cause as articles are introduced for cleaning.